World’s First Spiral-Welded Wind Tower Begins Operation
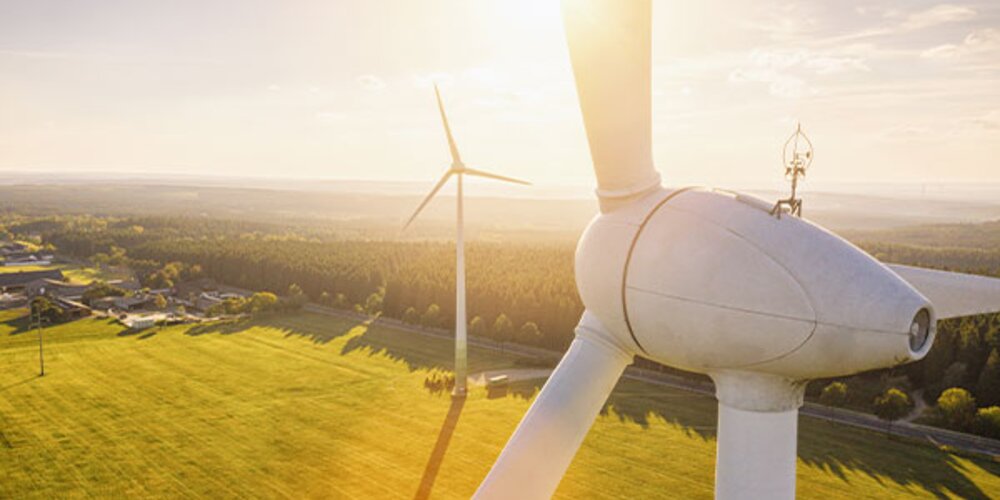
The world’s first spiral-welded wind tower has entered operation, signalling a major step forward for a welding technique that could drastically reduce the construction and fabrication costs of wind turbines.
The wind tower in question has been developed following a multi-year partnership between Keystone Tower Systems and GE Renewable Energy to advance spiral-welding techniques.
Borrowed from the steel-pipeline industry, spiral-welding allows manufacturers to construct wind turbines from metres-wide steel plate which is curled into a cylinder which is then welded.
Coils of steel plate are fed into angled bending machines that bend them into a spiral shape. As the spiral takes form, a weld is made along the join line continuously as the steel plate is turned.
The technique requires only a single machine to construct a wind turbine tower. Additionally, the technique allows manufacturers to fabricate towers up to twice as tall and 10 times faster than conventional techniques.
Additional savings are expected to accrue as the welding process is largely automated. In fact, Keystone claims that their technique requires 80% less manpower.
It is hoped that this new spiral-welding fabrication technique will make wind power exceptionally economical. As Keystone’s co-founder and CTO, Eric Smith, says:
“This is the culmination of a dream we had to bring advanced manufacturing to the tower industry to help drive down the cost of wind energy and expand where wind is competitive into new regions.
I’m very proud of the years of hard work our team has invested in developing and scaling up tapered spiral welding”.
Whilst the first spiral-welding wind tower was constructed at Keystone’s factory in Pampa, Texas, the company is now developing mobile factories capable of building towers directly on site at wind farms.
In need of weld testing services?
Then speak to The Lab. Our NDT experts are adept of testing welds of all kinds in multiple contexts and settings.
We are able to work with you to deploy a range of weld testing methods to get the answers you need.
Some of the weld testing methods we are able to deploy include (but are not limited to):
- Visual testing.
- Magnetic particle testing.
- Liquid penetrant testing.
- Ultrasonic testing.
- Phased Array Ultrasonic Testing (PAUT).
- Magnetic Flux Leakage (MFL).
Discover The Lab’s full range of weld testing services now
For more materials science and NDT insights and news, explore The Lab’s News and Knowledge Hub…
Glossary of Metallurgy Terminology | What Is Non-Destructive Testing (NDT)? | Has the Secret of ‘Self-Healing’ Roman Concrete Been Revealed?
- Author
- Caroline Young
- Date
- 01/03/2023