Glossary of Metallurgy Terminology
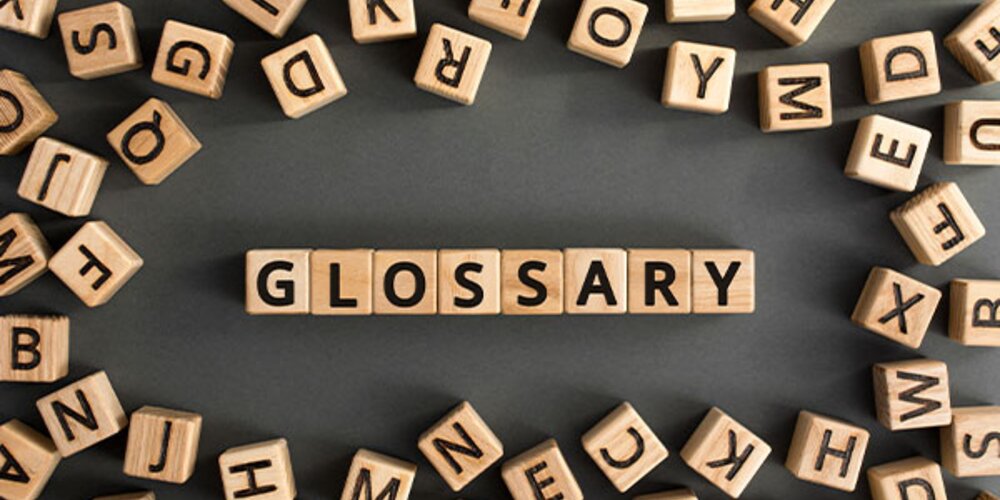
Metallurgy is a science which encompasses a huge range of topics - from the study of how metals interact with the various environments they find themselves in - to how metals can be used to fabricate useful components and structures. Because of this, metallurgy is awash with terminology.
To find out more about this terminology, read The Lab’s glossary of metallurgy terminology now…
A
Abrasion
Abrasion refers to the detachment or displacement of metallic particles from a metal as a result of exposure to flowing solids, fluids, or gases.
Abrasion resistance
Abrasion resistance is defined as the degree of resistance a metal has against abrasion or wear.
Acid embrittlement
Acid embrittlement is a process whereby brittleness is induced in metals as a result of the metal being immersed in an acidic solution.
Age hardening
Age hardening - which is also known as precipitation hardening - is a form of heat treatment that is used to impart strength to metals and their alloys.
Ageing
Ageing refers to the process whereby metals change their properties following changes in temperature. Ageing occurs slowly at room temperature, but more rapidly at higher temperatures.
Changes in properties are often (but not always) as a result of a phase change - but do not result in changes to the chemical composition of a metal or its alloy.
Air scale
Air scale is a type of scale that is typically left on ferrous metals following processing. It usually occurs from heating in the presence of air.
Alloy
An alloy is a substance which has metallic properties and is composed of two or more chemical elements (one of which is a metal). An alloy will normally have characteristics that are different from its constituent elements.
Annealing
Annealing is the process of heating a metal to a suitable temperature (and maintaining that temperature), followed by cooling at a rate that lowers the hardness or other mechanical or physical properties of a metal.
Austenite
Austenite is defined as a solid solution of largely iron and carbon, with a face-centred cubic crystal structure. Austenite is also known as gamma-phase iron (y-Fe).
B
Bimetal
Bimetal refers to an object which is composed of two separate metals which have been joined together. Bimetals differ from alloys in that their metals are layered rather than being mixed together.
Bright annealing
Bright annealing is a type of annealing that is carried out in a vacuum or controlled atmosphere containing inert gases. This controlled atmosphere minimises surface oxidation, resulting in a metal with a much brighter surface.
Bulk density
Bulk density refers to the mass of the particles of a material divided by the total volume they occupy. Bulk density is sometimes also called ‘apparent density’ or ‘volumetric density’.
Burnishing
Burnishing is a finishing technique that involves tumbling or rubbing a piece of metal using a polishing hand tool in order to achieve a smooth finish.
C
Carbide
A carbide is a compound of carbon that features one or more metallic elements.
Carbiding
Carbiding - also known as carburizing - is the process of producing carbide coatings on a piece of metal or metal component. The process involves subjecting a metal to a heat treatment process whereby the metal absorbs carbon.
Carbon
Carbon is an element which is typically found in the form of graphite or diamond. Though classed as non-metallic, it is treated as a metal by metallurgists.
Case-hardening
Case-hardening is a group of processes that are designed to substantially harden the outer surface of a ferrous alloy. Case-hardening processes include carburizing, carbonitriding, and nitriding.
Chemical (extractive) metallurgy
Chemical metallurgy is a branch of metallurgy that looks at the processes by which metals are separated by their ores and turned into useful materials.
Cohesion
Cohesion refers to the force by which the particles of a metal are held together. Cohesion varies from metal to metal and will depend upon the molecular arrangement of the metal as a result of heat treatment.
Constituent
A constituent is a micrographically distinguishable part of an alloy or mixture. In other words, a constituent is a part of a metal which can be identified by, and studied under, a microscope.
Corrosion
Corrosion is defined as a natural process that gradually deteriorates a metal via chemical or electrochemical interaction.
D
Decarburization
Decarburization refers to the loss of carbon from the surface of a ferrous metal. This loss of carbon is the result of heating in a medium that reacts with carbon (e.g. oxygen).
Degassing
Degassing is a process used to remove gases from a metal. The process involves inducing a chemical reaction by adding a compound to molten metal. Inert gases are typically used in this process.
Dendrite
A dendrite, in the context of metallurgy, is a tree-like structure of crystals that grows as molten metal solidifies. The way in which dendrites branch and grow has considerable consequences for the material properties of a metal.
Deoxidation
Deoxidation refers to the process of removing excess oxygen from a metal. This process is carried out by adding materials that have an affinity for oxygen. These materials will either neutralise the effects of oxygen, or directly remove the oxygen.
Die casting
Die casting - also known as pressure die casting - is a rapid permanent mould casting process that is used with non-ferrous metals. Molten metal is forced, under high pressure, into a mould cavity.
The two main types of die casting are; hot-chamber die casting, and cold-chamber die casting.
E
Elastic limit
The elastic limit of a metal is the maximum stress that it can withstand, without suffering permanent deformation.
Embrittlement
Embrittlement refers to a metal’s loss of ductility as a result of a chemical or physical change. An embrittled metal will fail by fracture without deforming.
End-quench hardenability test
The end-quench hardenability test is a standardised method to allow the hardenability of steels to be compared.
F
Fatigue
Fatigue is defined as the loss of load-bearing ability by a material (such as a metal). The loss of load-bearing ability is typically induced by repeated application of a load. Fatigue can ultimately lead to fractures.
Fatigue limit
The fatigue limit is the maximum stress that a material or metal can withstand (without failure), over an infinite number of load cycles.
Fatigue strength
Differing from fatigue limit, fatigue strength refers to the maximum stress a material or metal can withstand (without failure), for a specific number of load cycles.
Ferrite
Ferrite is defined as a ceramic compound that consists of a mixed oxide of iron and small amounts of other metals. Ferrite has ferrimagnetic properties, meaning it can be magnetised.
Ferritic steels
Ferritic steels are steels in which ferrite is the dominant phase. Ferritic steels are one of the five stainless steel families - the others being austenitic, martensitic, duplex stainless steels, and precipitation hardened stainless steels.
Frictional wear
Frictional wear is a type of wear that involves the displacement and/or detachment of metallic particles from a metal’s surface as a result of frictional contact with another surface.
G
Granular fracture
A granular fracture - also known as a crystalline fracture - is a type of fracture which has a rough, grain-like appearance. Granular fractures can be subdivided into transgranular and intergranular forms.
H
Hardenability
Hardenability refers to the degree to which a metal is resistant to indentation. There are a number of hardness scales including Brinell, Rockwell, and Vickers. Hardness can also refer to a material’s stiffness, and its ability to resist scratching, abrasion, and cutting.
Heat treatment
Heat treatment is defined as a series of heating and cooling operations that are undertaken to impart desired properties and microstructures to a metal.
Homogenization
Homogenization - or diffusion annealing - is a form of heat treatment at high temperature designed to remove chemical inhomogeneity that occurs in certain processes (e.g. heavy alloy steel casting).
Put simply, homogenization is a treatment which makes the composition/structure of a metal uniform.
Hot tear
A hot tear is a discontinuity that occurs during the solidification of a metal (typically during a casting operation).
Hot tears tend to occur because some form of force or restraint impedes the contraction of a metal as it cools - resulting in a hot tear. Hot tears can render a metal completely defective.
I
Impact strength
Impact strength measures a material’s resistance to impact loads. These loads are usually measured in the foot pounds of energy a material can absorb until it fails (e.g. fractures or tears).
Impact value
Impact value measures the total energy required to break a metal or material via a single blow. The different types of impact value tests include the Charpy test and the Izod test.
Impregnation
Impregnation refers to the treatment of castings with a sealing medium to prevent things like pressure leaks. The types of sealing mediums used can include silicate of soda, drying oils, plastics and various proprietary compounds.
Impurity
In metallurgy, an impurity refers to an element which has unintentionally found its way into an alloy or metal. The type and extent of impurity can have a greater or lesser impact on the characteristics of a metal or alloy.
Inclusions
Inclusions are non-metallic materials that can be present in metals and alloys. Inclusions typically find their way into a metal or alloy during the melting and pouring process. Depending on their origin, inclusions can be either endogenous or exogenous.
Induction hardening
Induction hardening is a type of surface hardening process that uses localised pulses of magnetic currents to heat the subject metal.
The metal is heated above the austenite transformation temperature (Ac3), followed by quenching. This brings about the hardening of the metal’s surface.
Intergranular corrosion
Intergranular corrosion - also known as intergranular attack - is a type of corrosion where the boundaries of the crystallites of a metal are attacked. Such corrosion is localised at and adjacent to grain boundaries - with little to no corrosion at the grains themselves.
Isothermal transformation
An isothermal transformation is a phase transformation that occurs at a constant temperature.
J
Joint welding
Joint welding is a type of production welding that is used to weld two or more individual metal components or pieces together.
K
K Factor
The K Factor refers to the ratio between a material’s thickness and its neutral fibre axis (also known as the part of a material that is bending without compressing or being elongated).
The K Factor can be calculated by taking a material’s tensile strength in pounds per square inch and dividing it by the material’s Brinell Hardness number.
Kayser Hardness Test
The Kayser Hardness Test is a test that is used to determine the true hardness of a metal at high temperatures.
L
Lateral expansion
Lateral expansion is a characteristic that is measured in the Charpy impact test. Lateral expansion refers to the increased width of a specimen after it has been fractured in the test.
M
Martempering
Martempering - which is also known as interrupted quenching - is a form of heat treatment which is designed to harden a metal. It involves slowly cooling a metal through the martensitic transformation range, reducing the stresses that are involved with the quenching of austenite.
Martensite
Martensite is a very hard steel crystalline structure. The term martensite can refer to any crystal structure that is formed by diffusionless transformation.
Martensitic stainless steel
Martensitic stainless steels are steels which are characterised by a predominant martensitic phase. Martensitic stainless steels are corrosion-resistant alloys.
Mechanical metallurgy
Mechanical metallurgy is concerned with the mechanical aspects of working with metals such as rolling, forging, extrusion, spinning, stamping, machining and more.
Metallurgy
Metallurgy is the study of the exploitation of metals. It includes the study of the extraction of metals from their ores, their refinement, and combination into useful alloys, and the measurement of their physical, mechanical and chemical properties.
Microshrinkage
Microshrinkage is a form of very finely divided porosity in a metal. Microshrinkage is a result of interdendritic shrinkage, with etching showing that this shrinkage occurs at the intersections of convergent dendritic directions.
Microshrinkage is usually a result of a casting defect, whereby contraction occurs during solidification with insufficient opportunity to supply filler material to compensate for shrinkage.
N
Negative quenching
Negative quenching refers to the rapid cooling of a metal in water or oil. This type of quenching takes place from a temperature below the critical range.
Nitriding
Nitriding is a surface hardening process that involves heating the metal in an atmosphere of ammonia (or whilst in contact with a nitrogen-bearing material). The result is that the metal absorbs nitrogen, becoming harder and more resistant to wear and abrasions.
Non-Ferrous
Non-Ferrous refers to an alloy in which the predominant metal is not iron.
Normalising
Normalising refers to the process of heating a ferrous alloy to an elevated temperature, then slowly cooling it down to room temperature.
This process changes the microstructure of the alloy, reducing its hardness and increasing its ductility.
O
Oxidation
Oxidation refers to any reaction of an element with oxygen. In metallurgical terms, oxidation can refer to a form of corrosion at high temperatures (in the absence of water or an aqueous phase).
Oxide
An oxide is a compound of oxygen with another element.
Oxidising atmosphere
An oxidising atmosphere is a gaseous atmosphere in which an oxidising reaction can occur.
P
Passivity
Passivity refers to those metals that develop a layer of metal oxide on their surface. This layer of metal oxide reduces (or completely stops) electrochemical reactivity, decreasing the corrosion rate of the underlying metal.
Physical metallurgy
Physical metallurgy is the science and study of the physical and mechanical characteristics of metals and alloys.
Pitting
Pitting is defined as a type of wear that results in surface cavities on a metal or alloy. The formation of these ‘pits’ can be the result of corrosion, fatigue, cavitation or local adhesion.
Precipitation hardening
Precipitation hardening - which is also called age hardening or particle hardening - is a form of heat treatment that is used to increase the strength of malleable alloys such as aluminium, magnesium, and nickel (amongst others).
Q
Quenching
Quenching is the rapid cooling (hardening) of a metal. This cooling is normally achieved by submerging the metal in water, oil, or solutions of organic compounds.
R
Recrystallisation
Recrystallisation is a process where the distorted grain structure of a metal is replaced by defect-free grains. These defect-free grains nucleate and grow until they have replaced the original - defective - grains.
The recrystallisation of a metal will sometimes also see the strength and hardness of a metal diminish, along with a corresponding increase in ductility.
Reduction
In metallurgical terms, reduction refers to either the removal of oxygen or the addition of hydrogen to a metal.
Refractory
A refractory is a material that is resistant to decomposition - most notably by heat, but also by pressure or chemical attack. Refractories are used in a wide range of metallurgical assets, such as furnaces.
S
Scaling (scale)
Scaling is defined as surface oxidation that is left on metals following heating or casting in air or other oxidising atmospheres.
Segregation
Segregation is the situation where a concentration of alloying elements occurs at specific regions within a component or sample. Segregation is usually the result of the primary crystallisation of one phase, and the latter concentration of other elements in the liquid that remains.
Shear
Shear refers to the lateral shifting of a metal’s inter-granular plates in relation to each other. Shear can also refer to a type of load which can induce a material failure along a parallel plane.
Shear strength
Related to shear, shear strength is defined as the amount of shear stress that a material can withstand without failing.
Shot blasting
Shot blasting is a cleaning technique that uses steel particles (e.g. shot) which are blasted at a material via air or centrifugal force. Shot blasting is typically used to smooth out a rough surface, or to remove paint or contaminants from a material.
Shrink
Shrink refers to the difference in volume between a liquid metal and a solid metal.
Shrinkage
Related to shrink, shrinkage is the series of stages a metal goes through as it cools from liquid to metal.
Skin
A skin is a thin surface layer which is physically or chemically different from the object it is covering.
Smelting
Smelting is a metallurgical process whereby metal is separated (in fused form) from non-metallic materials.
Stainless steel
Stainless steel is a term that refers to a wide range of steels that are alloyed with chromium, or chromium and nickel. Stainless steels are noted for their high resistance to corrosion.
Steel
Steel is an alloy of carbon and iron (although it can also contain other elements). The carbon content of steel is usually less than a few tenths of a percent.
Stress-corrosion cracking
Stress-corrosion cracking refers to the spontaneous failure of metals by cracking. The cracking is typically induced by a combination of corrosion and stress - either residual or applied.
T
Tempering
Tempering is a form of heat treatment which is used to increase the impact strength of iron-based alloys.
Tempering typically involves heating a metal to below its critical range, then allowing it to cool in still air.
Tensile strength
Tensile strength refers to the maximum load that a metal or alloy can withstand without fracture - whilst it’s being stretched or pulled.
Thermal conductivity
Thermal conductivity is a measure of the ability of a metal to conduct heat. In pure metals, thermal conductivity stays relatively constant across increases in temperature.
Thermal contraction
As the name suggests, thermal contraction is a measure of the decrease in a linear dimension and volume of a metal or alloy as per a change in temperature.
Thermal expansion
Thermal expansion is a measure of the increase in a linear dimension and volume of a metal or alloy as per a change in temperature.
Thermal fatigue
Where a metal or alloy fails as a result of rapid cycles of alternate heating and cooling, it is said to have experienced thermal fatigue.
Toughness
In metallurgical contexts, toughness is defined as the ability of a metal or alloy to absorb energy and plastically deform, without fracturing.
Transformation range
The transformation range is the critical temperature at which a change in phase occurs in a metal.
The critical points in heating and cooling are referred to respectively as Ac points (c for Chauffage or heating) and Ar points (r for Refroidissement or cooling).
Tribology
Tribology is defined as the science of interacting surfaces in motion. It examines the application and principles of friction, wear, and lubrication in relation to interacting surfaces in motion.
U
Ultrasonic inspection
Ultrasonic inspection covers a range of non-destructive tests that use ultrasonic waves to analyse samples/objects/components. These tests include; pulse echo (PE), through transmission (TT), and time of flight diffraction (ToFD).
V
Virgin metal
Virgin metal - alternatively known as primary metal - is a metal which has been directly extracted from the ore and has not previously been used.
Void
In metallurgical terms, a void is a shrinkage cavity which is produced during casting as a metal solidifies.
W
Wear
Wear can be considered as the undesired deterioration of a metal, via the removal of material from its surface.
Welding
Welding is the process by which metals are joined together via the application of heat. Gas, arc, and resistance welding (which are forms of fusion welding), melt the parent metals as part of the welding process.
X
X-ray diffraction
X-ray diffraction analysis is a non-destructive test that is used to analyse the structure of crystalline materials. The process involves bombarding a sample material at different angles with x-rays.
Y
Yield
Yield is defined as the comparison between casting weight, to the total weight of metal that was originally poured into the mould.
Yield ratio
The yield ratio refers to the ratio of the yield strength to the ultimate tensile strength of a metal or alloy.
In need of metallurgy services?
Whether you need to identify a material or require non-destructive tests of varying types, The Lab can help.
We work with businesses large and small across the maritime, energy, manufacturing, automotive and many other industries to support them with their forensic investigation requirements - no matter how challenging.
For a free, no-obligation consultation about your requirements, contact The Lab today.
Speak to The Lab and find out how we can help you today
For more materials science, materials testing and NDT insights, explore The Lab’s News and Knowledge Hub…
What Is Non-Destructive Testing (NDT)? | Why Bunker Fuel Analysis Is More Important Than Ever | What Is Metallurgy and How Is It Used in the Maritime Industry?
- Author
- Dr Holly Edwards
- Date
- 25/11/2022