What Is Non-Destructive Testing (NDT)?
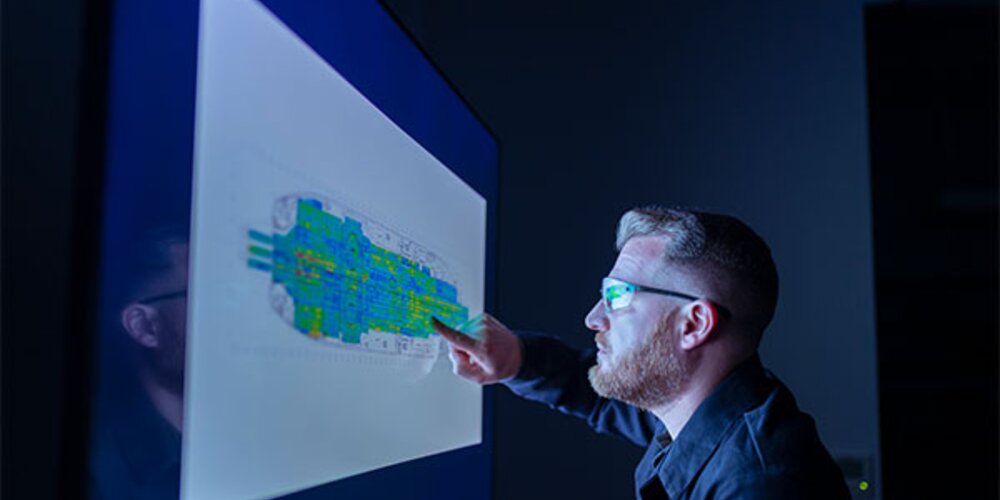
If you’re looking to investigate the integrity and condition of a material then one of the best ways of doing so can be via what’s called non-destructive testing. More commonly known by the initialism ‘NDT’, non-destructive testing encompasses a series of tests that are used throughout the maritime, energy, engineering and many other industries. If you want to know more about NDT, then keep reading…
What is non-destructive testing?
Let’s begin with a high-level definition.
Non-destructive testing is a form of testing and analysis that examines the properties of a material, asset, component, part or structure in such a way as to yield useful insights, without destroying the material itself.
In other words, NDT allows you to investigate materials without destroying them. As such, NDT has become a highly-valued form of material testing, and as we said at the outset, has been applied in a vast array of different industries across the world.
Note - non-destructive testing is sometimes also called non-destructive examination (NDE), non-destructive evaluation (NDE) or non-destructive inspection (NDI).
What’s the difference between non-destructive testing and destructive testing?
Forgive the rather obvious question, but it’s important to differentiate between NDT and destructive testing.
Destructive testing is a form of testing and analysis which, while yielding useful insights, results in the eventual destruction of the material/asset/part/component that’s being tested.
Examples of destructive tests include:
- Fatigue testing - which involves applying cyclic loading to a material or component.
- Hardness testing - which involves testing a material to determine its resistance to permanent deformation.
- Aggressive environment testing - this form of testing can involve exposing a material to highly aggressive environments e.g. extreme pressure, extreme temperatures, highly corrosive environments etc.
- Torsion testing - a test whereby ‘twisting’ forces are applied to a material until it succumbs to twisting, marking the failure point.
These are just a few examples of the types of destructive testing methods. However, they should make clear the very distinct difference between NDT and destructive testing.
What are the different types of non-destructive testing?
As we mentioned earlier, non-destructive testing doesn’t refer to a single form of testing, but a group of tests which share the common theme of not destroying the sample/material they are testing.
There are tens of different NDT methods available, covering specific types of technologies and methodologies including visual inspection, electromagnetic testing, radiographic testing, leak testing and more.
Below, we’ve set out some of the most commonly used forms of non-destructive testing.
Electromagnetic testing (ET)
As its name suggests, electromagnetic testing involves the passing of an electric current (or magnetic field) through a material which is conductive.
There are a number of different tests which fall under the umbrella of electromagnetic testing:
- Eddy current testing.
- Pulsed eddy current testing.
- Alternating current field measurement (ACFM).
- Remote field testing (RFT).
What is eddy current testing?
Eddy current testing is a form of electromagnetic testing that’s used to detect flaws in materials, as well as determining material and coating thickness, the identification of materials and more.
Eddy current testing works by passing an alternating current through a conducting material. This induces an alternating magnetic field around the conducting material. This field expands and contracts as the alternating current rises and falls.
If the conducting material is placed close enough to another conductor, this causes the magnetic field to pass through this second conductor, thus inducing an eddy current. This eddy current develops its own magnetic field.
With these two opposing magnetic fields, samples can be examined. Should the material possess any near-surface defects or differences in thickness, this will affect the magnitude of the eddy current - therefore eddy current testing can detect defects in materials without destroying them.
What is pulsed eddy current testing (PEC)?
Pulsed eddy current testing is an electromagnetic testing technique which is particularly useful for detecting corrosion and flaws on materials which are hidden under coatings or layers of insulation.
This inspection technique works by creating a magnetic field. This magnetic field is then used to inspect an asset, with the field passing through any non-conductive surface (e.g. concrete, silicate, marine growth and more).
Once the field has stabilised, the current generating the field is turned off. This causes eddy currents which are then captured by a probe. Most pulsed eddy current probes will measure the decay rate of these eddy currents - leading to an accurate analysis of the condition of the material/surface/asset under inspection.
What is alternating current field measurement (ACFM)?
Primarily used to detect surface-breaking discontinuities in materials, ACFM has its roots in eddy current testing.
ACFM works by using a probe to introduce an electric current into a sample. It then measures electromagnetic fields close to the surface of the material.
If the material has a defect, this disturbs these electromagnetic fields - which are then communicated via the probe to the operator.
What is remote field testing (RFT)?
Primarily used to detect defects in steel pipes and tubes, remote field testing (RFT) uses a similar - but different - technique to eddy current testing.
RFT works by generating an alternating current. This current is then released through a coil which is placed within the tubing that’s been inspected. Whilst this sounds similar to current eddy current testing, RFT differs in that it uses a different frequency of AC.
RFT also tends to be used to detect different types of faults to eddy current testing. RFT can be used to detect faults on both the inside and outside of tubing.
Ground penetrating radar (GPR)
Ground penetrating radar, as you may have guessed by its name, is a form of non-destructive testing that is used to investigate the surface of a material which is located in a subsurface environment (e.g. a pipe that’s buried beneath the ground).
GPR works by transmitting high-frequency radio waves through a material in order to reach the surface which is being inspected.
In NDT contexts, GPR is primarily used for detecting the dimensions and thickness of materials that are located underground or beneath other similar surfaces.
Laser testing methods (LM)
Laser testing for non-destructive testing consists of three separate techniques:
- Holographic testing.
- Laser profilometry.
- Laser shearography.
What is holographic testing?
Holographic non-destructive testing involves the use of a large ultrasonic transducer to send out ultrasonic waves which are generated and detected by lasers.
Holographic testing can be used for thickness measurement, flaw detection and material characterisation and is particularly useful for detecting changes in the surface of a material which are a result of stress, heat, pressure or vibration.
What is laser profilometry?
Laser profilometry uses what’s called a laser profilometer (or laser mapper) to scan the surface of a material.
The laser beam passes over the surface, with the distance of the beam being measured and interpolated into a 3D image based on the topography of the surface.
This form of laser inspection is not only quick and carried out with relative ease, but allows for very large amounts of data to be captured and processed regarding a material’s surface.
In recent years, laser profilometry has found widespread use in the non-destructive testing and inspection of pipelines and other related assets.
What is laser shearography?
Laser shearography involves the use of a laser to inspect a surface. A sheared reference image is taken with the surface/structure then stressed.
The laser is then used to produce another post-stressed image which is compared to the original image. The two images are then compared in order to detect if there are any defects present in the material/sample.
Leak testing (LT)
Leak testing is a testing technique which allows you to determine whether an asset or system is functioning within a specific leak limit.
As you would expect, leak testing is predominantly used to test systems or assets which are used to store or move liquids or gases.
Leak testing consists of a number of distinct leak testing methods, including:
- Bubble leak testing - where a liquid or soap is applied to a system/surface to detect leaks in the form of bubbles.
- Pressure change testing - also known as pressure decay testing, this test involves filling a closed pressurised system with air until it reaches a target pressure. The system is then isolated, with the loss of pressure (if any) then measured over a set period of time.
- Halogen diode testing - similarly to pressure change testing, halogen diode testing involves pushing a mix of air and halogen tracer gas through a pressurised system. A halogen diode detection sniffer tool is then used to locate any leaks (picking up on trace amounts of the air and hydrogen tracer gas that may have escaped the system).
- Mass spectrometry leak testing - arguably the most sensitive form of leak testing, mass spectrometry leak testing uses a mass spectrometer to detect a helium (or an air or helium mix) tracer gas which may be leaking from a system.
Magnetic flux leakage (MFL)
Predominantly used to detect corrosion and pitting in steel structures, magnetic flux leakage tests involve the use of magnetising a ferrous metal object (i.e. the asset being tested) with a magnetic field until it reaches ‘saturation ‘level’ (i.e. the asset has absorbed the maximum amount of magnetic force it can).
A magnetic sensor will then be placed between the poles of a magnetic yoke to detect changes in magnetic flux density. For example, where corrosion or pitting has occurred, this will lead to the ‘leakage’ of the magnetic field from the asset.
Microwave testing
Used on materials which are poor conductors of electricity (e.g. dielectric materials), microwave testing involves the transmission of microwave frequencies through a material. The transmitted microwave frequencies are then picked up by a probe.
It’s the job of the probe to detect any changes in dielectric properties that have occurred in the material that’s being tested. These dielectric changes can include shrinkage cavities, pores, cracks and more (by dielectric changes we are referring to changes to a material’s ability to impend electron movement).
Liquid penetrant testing (PT)
When you need to check for deficiencies and faults in a pipe or weld, liquid penetrant testing represents a relatively quick way of doing so.
Liquid penetrant testing (also known as dye penetrant testing, dye penetration testing, and liquid penetrant examination), begins with the surface in question being prepared. This is followed by the application of a low-viscosity liquid penetrant.
The liquid penetrant then works its way through the material/sample/asset. Once it has done this, a developer is applied which allows the penetrant to seep upward into any cracks or similar defects, making them visible to the inspector.
Magnetic particle testing (MT)
Magnetic particle testing (also known as magnetic particle inspection), is primarily used to detect surface and subsurface flaws such as cracks in ferromagnetic materials.
This method of testing involves the use of a magnet or electromagnet to create a magnetic field (via the application of a current to the magnet or electromagnet). This field is then passed into the sample being inspected.
This creates a magnetic flux throughout the surface of the sample. If the sample has a subsurface discontinuity, this allows the magnetic flux to leak.
In order to detect such leaks, ferrous particles will be applied to the sample. If these are attracted to an area where the magnetic flux is leaking, this indicates the presence of a leak or discontinuity in the sample.
Neutron radiographic testing (NR)
Used to a limited extent in the maritime, energy and manufacturing industries, neutron radiographic testing involves the use of neutrons - shooting a beam of them through a sample.
As the beam of low-energy neutrons interact with the sample, some neutrons will pass through whilst others will not. Those that do pass through hit an imaging agent. This imaging agent then creates an image of the sample’s interior (this image is often referred to as an ‘attenuation pattern’).
This image or pattern can then be analysed to identify flaws within the sample.
At present, neutron radiographic testing isn’t widely used. This is largely down to a lack of sources of neutrons.
Radiographic testing (RT)
Similar to neutron radiographic testing, radiographic testing uses beams of radiation to analyse samples and detect defects.
Where radiographic testing differs from neutron radiographic testing is that the former tends to use x-rays or gamma rays rather than the neutrons of the latter.
X-rays tend to be used where the sample is relatively thin, whilst gamma rays are used where a sample is denser.
The test works by placing the sample between the source of the radiation beam and a film (or detector). As the beam passes through the sample it becomes attenuated. This attenuation is then recorded on the film or detector, providing an image which can be analysed to detect faults and defects.
Whilst we mentioned film or detectors above, there are in fact several imaging methods used for radiographic testing including film radiography, real-time radiography (RTR), computed tomography (CT), digital radiography (DR), and computed radiography (CR).
Thermal infrared testing (IRT)
Thermal infrared testing uses infrared cameras to detect radiated thermal energy from objects.
It’s an NDT technique which finds particular use for building diagnostics, as it allows inspectors to detect heat or cooling loss as well as moisture loss as a result of construction issues or asset/material failure.
Likewise, thermal infrared testing also finds extensive use in industries such as the maritime industry, where it can be used to detect overheating bearings, motors or other components.
Ultrasonic testing (UT)
Ultrasonic testing encompasses a series of related tests that use ultrasonic waves in order to analyse samples/objects.
Ultrasonic testing can be divided into three separate tests:
- Pulse echo (PE).
- Through transmission (TT).
- Time of Flight Diffraction (ToFD).
What is pulse echo testing?
Pulse echo testing involves the use of sound beams, which are beamed into a sample.
The sound beam will travel until it reaches the rear wall of the sample. It’ll then return to the transmitter. If there is a discontinuity within the sample though, the beam will return to the transmitter early.
Based on the acoustic velocity of the sound beam, the time interval between the emission of the beam and its return allows for the location of the discontinuity to be calculated.
What is through transmission testing?
In contrast to pulse echo inspection, through transmission testing involves the use of two transducers to create and receive sound beams.
One probe, which acts as the transmitter, is positioned on one side of a sample, whilst the other probe, which acts as the receiver, sits on the other side.
A sound beam is then passed through the sample. If the passage of the beam is interrupted, this indicates the presence of a flaw within the sample.
What is time of flight diffraction (ToFD)?
Another method of ultrasonic testing is known as time of flight diffraction. With this method, two probes are placed either side of a sample (one that acts as a transmitter, another that acts as a receiver).
Where time of flight diffraction differs from other forms of ultrasonic testing is in its use of two distinct waves - a lateral wave (which travels along the surface of the sample), and another wave which reflects off the back of the sample.
Should these waves encounter a fault or discontinuity in the sample, then this will cause the ultrasound pulses to diffract from the edges of the fault. In other words, an ultrasonic beam is used to find the location of a reflector (i.e. a fault).
Advanced ultrasonic inspection
Advanced ultrasonic inspection methods represent the very latest development in ultrasonic inspection techniques, with phased array ultrasonic testing (PAUT) being one of the most prominent techniques in use across many industries.
What is phased array ultrasonic testing (PAUT)?
Unlike more basic forms of ultrasonic testing, phased array ultrasonic testing makes use of multiple transducers - each of which can emit pulses independently.
These multiple transducers are typically operated in such a way as to emit pulses in a progressively delayed line, creating a pattern of constructive interference.
This results in the emission of a larger ultrasonic beam (made up of the individual beams from each transducer) which passes through the sample at an angle (this angle can vary depending on the time delay of each individual transducer).
Because the beam angle and focus distance can be tightly controlled, PAUT is a very efficient and quick way of detecting faults in a material or asset.
What is full matrix capture (FMC)?
Another form of advanced ultrasonic inspection is what’s known as full matrix capture.
Considered to be an evolution of the PAUT technique, full matrix capture uses the same types of transducers as PAUT, but instead of requiring the beams to be steered around the sample, the entire sample is in focus at any one time.
This makes full matrix capture a fairly straightforward inspection technique; albeit, one that generates very large files and which can be slower than PAUT.
Vibration analysis
When it comes to monitoring the health of machinery such as motors, vibrations are often a warning sign of an impending failure or problem.
As such, vibration analysis is a highly effective NDT inspection technique.
Vibration analysis will normally involve the use of a series of sensors, including velocity sensors, accelerometers and displacement sensors.
Carried out when a piece of machinery is under load (i.e. in operation), vibration analysis will measure both the magnitude of vibration and the frequency spectrum of the vibration.
From these two measurements, a vibration analysis is able to identify how severe a vibration is, and the origin of the vibration.
Visual inspection
Visual inspection - which is also known as visual testing - is one of the most common and straightforward NDT techniques. In fact, it’s often referred to as the original form of non-destructive testing.
In its simplest form, visual inspection involves an inspector looking at a sample/component/asset etc. The operator may supplement this inspection with the use of a magnifying glass, microscope, or cameras.
Increasingly, visual inspections in hazardous environments (such as offshore) are being carried out via drones.
Are you in need of non-destructive testing services?
No matter what it is you need testing in a non-destructive fashion, The Lab can help.
Our team of highly-experienced NDT experts can inspect, test and evaluate materials, components, assemblies and assets to the highest standards.
The Lab’s non-destructive testing services cover a broad range of industrial scenarios and contexts and include:
- Weld testing methods.
- Heat transfer solutions - tubes.
- Cargo tank, pressure vessel and tanktainer inspection services.
- Corrosion under insulation (CUI) inspection services.
- Electromagnetic technologies for surface inspections.
- Electromagnetic technologies for tubing inspections.
- Full corrosion assessments.
To find out more about how The Lab’s industry-leading non-destructive testing services can benefit your business, speak to us today.
Explore The Lab’s non-destructive testing services now
For more materials science, materials testing and inspection insights and news, explore The Lab’s News and Knowledge Hub…
What Is Metallurgy and How Is It Used in the Maritime Industry? | What Are Materials Science and Materials Testing and Why Are They Important? | Is Carbon Neutral Concrete on the Horizon?
- Author
- Arron Jackaman
- Date
- 24/08/2022