LEBW Technique Used to Weld Full-Sized SMR Nuclear Vessel in 24 Hours
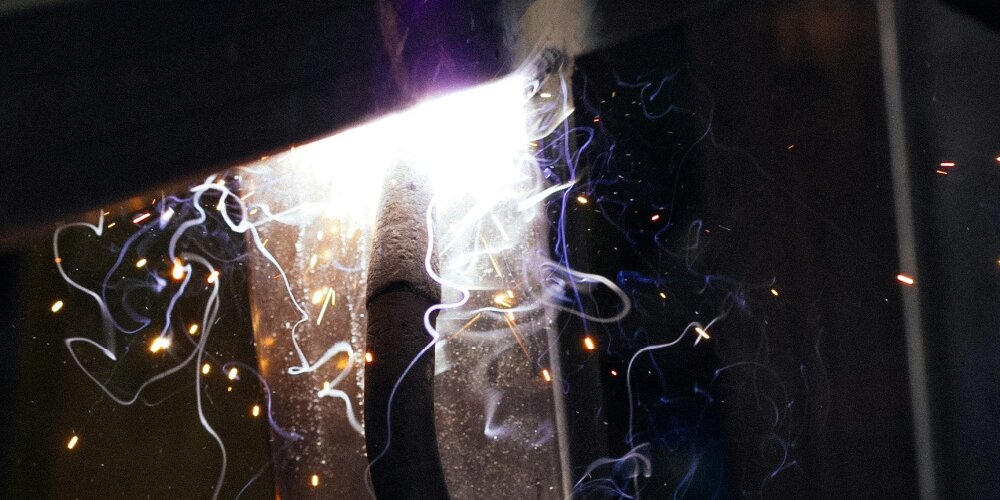
In a groundbreaking first, experts from Sheffield Forgemasters have built a full-sized SMR nuclear vessel in 24 hours using LEBW – or local electron-beam welding. This is a pivotal moment for welding technology and development, and sets a standard for the future of large-scale nuclear welding projects around the world.
An SMR, or ‘small modular reactor’, is a type of nuclear fission reactor that can generate anywhere from 5 MW up to approximately 300 MW of energy (with the higher end of the scale attributed to more commercial models).
Perhaps most importantly, SMRs are ‘modular’, which in this case means that they’re constructed in a factory before being shipped to their final location. Whilst usually these take around a year of intense labour to build, the team at Sheffield were able to fully weld one in less than 24 hours using the LEBW technique.
Most conventional welding techniques use the direct application of heat to melt and join two materials together, or to melt a consumable material between the two that creates a connection. Electron-beam welding, on the other hand, is slightly more complicated. This technique uses a high speed stream of electrons to create kinetic energy, which is then transformed into heat energy to melt materials at the join. Another aspect that makes this a more complicated technique is that it needs to happen in a vacuum, or the electrons collide with other particles in the air and lose their energy.
Overall, this type of welding is incredibly precise, and limits material distortion because it has a smaller heat field than other types of welding. Unfortunately, the relatively high cost of materials and maintenance has somewhat stymied efforts to make it more commercially available.
To mitigate these costs, recent developments have created a localised method, which allows the electron beam to be enclosed in a vacuum box on the side of the materials being welded, rather than enclosing the whole structure in a vacuum chamber. And it’s this method that the team in Sheffield used to great effect when constructing the SMR.
Alongside extensive planning, and using innovative sloping-in and sloping-out techniques, the team was able to create comprehensive, high-quality, and defect-free welds in a very short time.
In addition to being a huge leap in thick-walled structure assembly, the construction of a SMR in this timeframe also has big implications for the future of nuclear assembly.
Due to the high level of precision, minimal contaminants, and comprehensive welds, LEBW can have a big impact on how nuclear machinery is built. According to Dr. Michael Blackmore, the Senior Development Engineer, and Project Lead, local electron-beam welding has the potential to reduce high-cost welding processes, significantly speed up the construction process and deployment of SMRs, and even lower the need for equipment inspections in the future.
The whole feat is a massive milestone in the large-scale use of LEBW, and bodes well for the future of this welding technology, and for the construction of other thick-walled structures.
Looking for an exceptional non-destructive testing facility?
Understanding material behaviour is vital, but you don’t always want to deconstruct or disassemble your systems in order to conduct testing. Fortunately, at The Lab, we have a wide range of non-destructive testing services including a range of weld testing methods, to ensure you can continue to operate safely and effectively with minimal to zero downtime of your assets.
Contact us today for a no-obligation consultation to find out how non-destructive testing can benefit you.
Explore non-destructive testing at The Lab
For more advice, information, and valuable industry insights, explore The Lab’s News and Knowledge Hub…
Researchers Find New Way to Weld Metal Foam Without Compromising the Material | New 3D Printing Technique Developed to Print One of the World’s Toughest Steels | World’s First Spiral-Welded Wind Tower Begins Operation
- Author
- Arron Jackaman
- Date
- 20/05/2024