Researchers Develop Carbon Nanotubes for Non-Destructive Testing Method
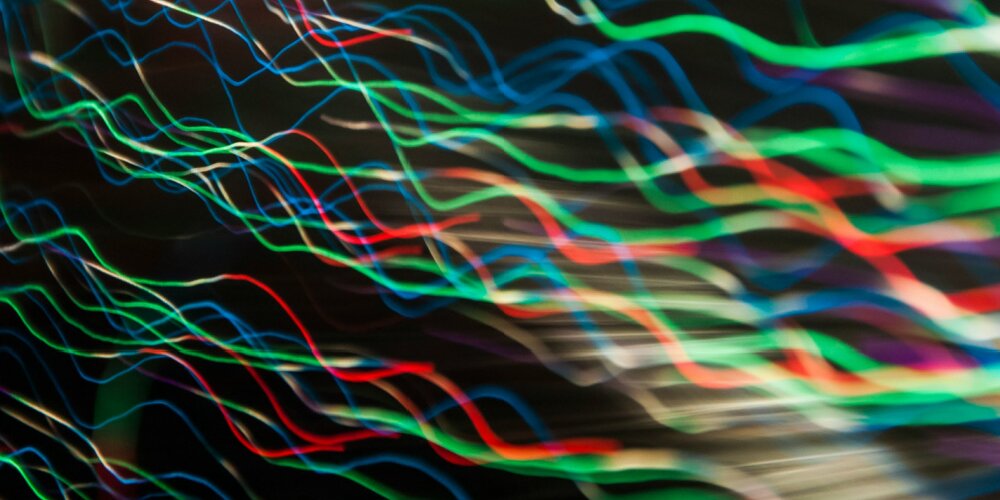
Researchers based at Chuo University in Japan have developed a novel new method to improve non-destructive capabilities using carbon nanotubes (CNT). Non-destructive testing (or NDT) is an incredibly important materials testing technique that allows you to gather data about a component – crucially without deconstructing it or taking it out of operation. This is vital for many industries, where removing components to conduct tests could cause large economic and production losses.
Instead, the research team has created a photosensitive device that combines carbon nanotubes and detailed photo-monitoring with 3D computer vision techniques designed to generate more in-depth and detailed reconstructions for engineers and scientists to examine for defects.
Previous uses of carbon nanotubes have shown how they’re able to exploit the photothermoelectric (PTE) effect, which combines photo-absorption, induced heating and thermoelectric conversion to gather information about material composition. The research team have taken this a step further however, as they explain that, ‘CNT film PTE imagers exhibit photo-detection sensitivities in broad millimetre-wave IR (MMW-IR) regions, and demonstrate non-destructive material identification via multiple-wavelength monitoring’, and that by ‘employing multiple CNT film imager sheets [they can] provide omni-directional viewing angles without blind spots for monitoring 3D objects’.
The pain points come from attempting to examine the internal qualities of a 3D object, as ‘information regarding the size or positioning of the respective inner elements of composite multi-layer 3D target objects is crucially missing.’ Essentially, whilst previous techniques have been able to analyse the outside of a component, understanding where potential defects may lie internally has been lost – particularly in structures made from a combination of materials (like metals, glass, plastics and semiconductors).
To counteract this, the team has trialled a solution involving the CNT sensor and computer vision (CV) in ultrabroadband and multi-wavelength bands. This gathers two-dimensional data and uses the computer to reconstruct this information from the hidden parts of a machine or component into a 3D multi-layered object. Considering it worked effectively on glass, semiconductors, plastic and metal, it bodes well for use on real-world machinery.
Combining these technologies is also a promising step towards the development of new and innovative non-destructive reconstructive techniques to provide analysts with accurate and more functional data.
The Lab: home of non-destructive testing
As we mentioned above, non-destructive testing is vital for industries or machinery where you can’t afford to stop service, or where component removal will have serious financial ramifications.
Instead, you should explore the various non-destructive testing services we offer at The Lab. With a broad range of inspection technologies available for use, our experts can examine materials in-situ to afford you the best chances of maintaining serviceability.
Discover our non-destructive testing services at The Lab
For more industry insights, advice, and information, explore The Lab’s News and Knowledge Hub…
LEBW Technique Used to Weld Full-Sized SMR Nuclear Vessel in 24 Hours | Researchers Find New Way to Weld Metal Foam Without Compromising the Material | What Is Non-Destructive Testing (NDT)?
- Author
- Arron Jackaman
- Date
- 25/06/2024