Is It Possible to Create Carbon-Neutral Steel?
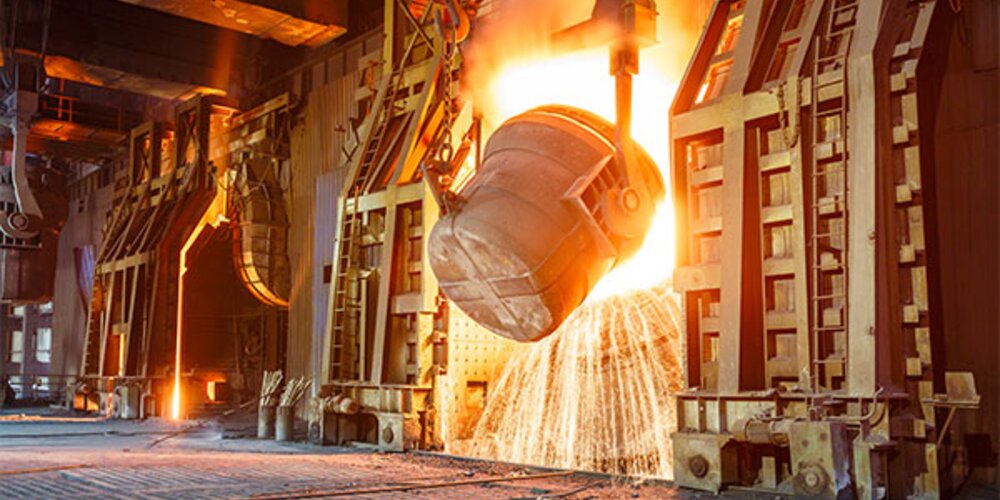
The world needs steel. From buildings to transport infrastructure, steel supports the modern world (literally). But, the production of steel is highly-carbon intensive. With policymakers pushing for a net-zero future, this poses a problem. The question is; is it possible to create carbon-neutral steel? The Lab investigates…
What is steel?
Steel is ubiquitous. Mention it to anyone you meet, and they’ll at least understand that you’re talking about metal.
But, what exactly is steel?
Steel is an alloy made up of iron with a small percentage of carbon. The carbon adds additional strength and imparts fracture resistance upon the steel.
Stainless steel is a high corrosion and oxidation resistant version of steel. It is corrosion and oxidation resistant due to around 11% chromium being added to the alloy.
Steel’s carbon emissions problem
Steel is arguably the world’s most important material. Used in everything from buildings to cars, to household appliances and cargo ships, it’s a material that humanity couldn’t do without.
To give you an idea of how much steel humanity requires, consider that world crude steel production reached 1,950.5 million tonnes in 2021.
Since 1970 global demand for steel has grown threefold, with demand not appearing to slow down any time soon, as emerging economies continue to grow and develop.
However, steel comes with a cost. Carbon emissions.
According to the International Energy Agency (IEA), the global steel making industry accounts for 2.6 gigatonnes of carbon dioxide (Gt CO2) every year.
Those emissions are directly associated with the way steel is produced, and the way the production process is powered.
Steel is produced in two main ways:
- Blast furnace-basic oxygen furnace (BF-BOF).
- Electric arc furnace (EAF).
Note - there are other steel production methods that are variations on the above ones, but these tend to be used on a more limited basis.
The blast furnace-basic oxygen furnace production method
The BF-BOF production method uses the raw materials of iron ore, and metallurgical coal (with scrap metal sometimes also added as an additional feedstock).
The raw iron ore is typically crushed and pelletised, whilst the metallurgical coal is turned into coke.
The ore and coke then go into a blast furnace (normally with the addition of limestone), and are heated to a very high temperature until glowing, liquid iron is produced. This liquid iron is accompanied by a by-product called slag - as well as huge amounts of CO2 emissions.
This pure iron is then heated until melting point is reached for a second time in a basic oxygen furnace (BOF). Whilst being heated in the BOF, oxygen is blown through a lance over the surface of the molten iron.
The oxygen creates an oxidation reaction, producing CO and CO2. This decreases the iron’s carbon content from approximately four percent, to less than one percent.
At this point, you have steel.
The problem is, this process involves the use of considerable amounts of carbon (in the form of coal).
Because iron ore is an iron oxide, to separate the iron from the oxygen, a reducing agent is needed. This reducing agent is carbon. During the reduction process, the carbon combines with the oxygen to form carbon dioxide (CO2).
Not only is coal used for this reduction process, but it’s also used to generate the high temperatures required in the blast furnace to smelt the iron ore.
In short, because carbon is essential to the reduction part of the BF-BOF production process, CO2 emissions are unavoidable in its present configuration. In other words, even if the power to generate the high temperatures for smelting could be sourced via renewable energy, carbon emissions will still result from this form of steel production.
The electric arc furnace production method
The EAF production method uses electricity to melt recycled steel. The electricity has no electrochemical effect on the metal, but simply heats it.
In some forms of EAF, the electricity is supplemented by oxygen in order to help accelerate decarburization.
Both of these processes use considerable amounts of energy.
According to the International Energy Agency, ‘the sector is responsible for about 8% of global final energy demand and 7% of CO2 emissions’.
That’s a considerable share of the world’s total carbon emissions.
But, given that we can’t do without steel - what’s the alternative?
Reducing steel’s carbon footprint
A variety of efforts are currently underway to reduce the carbon emissions associated with existing methods of steel production.
BF-BOF efficiency programmes
A series of BF-BOF efficiency programmes are currently underway, focused on either improving the efficiency of the process or decreasing production losses associated with the process.
These programmes include:
- Ensuring that the iron ores that are used have as high an iron content as possible. This reduces the amount of coal that is needed as a reductant.
- Increasing the use of fuel injection, with natural gas as an additional reagent on top.
These efforts have the potential to reduce carbon emissions associated with BF-BOF production, but not entirely eliminate them.
Carbon capture and storage
According to research conducted by McKinsey and others, carbon capture and storage is only currently used on a limited basis across the steel production industry.
Broader adoption of carbon capture and storage has the potential to allow steel producers to capture emissions and use them to create products for the chemical industry, such as ammonia or bioethanol.
Increased use of scrap-based EAFs
Electric arc furnaces already have fairly good production credentials, as they turn scrap steel into fresh steel - hence contributing to the ‘circular economy’.
As such, if EAF production can gain a larger share of overall global steel production, this should help ‘green’ the industry.
There are two important caveats to this, though.
Firstly, EAFs still do use considerable amounts of electricity. Increased EAF-based steel production will only be ‘green’ if the electricity it uses is generated by renewable sources. This requires the continued build-out of renewable power generating assets such as solar and wind farms.
The second caveat concerns the availability of scrap metal. The production of high-quality steel requires high-quality scrap. To date, this has been one of the biggest limiting factors to increased EAF production. In fact, demand for steel is projected to exceed scrap metal supply until at least 2050 (as per Pauliuk, et al. (2013)).
These are all worthy efforts, and if followed through, will contribute to significant reductions in the carbon emissions associated with global steel production.
The thing is - they’re not carbon-neutral.
So, is there really a viable carbon-neutral alternative to steel? One project in Sweden thinks the answer is ‘yes’.
Towards carbon-neutral steel
As we saw earlier, the crux of the problem is the use of carbon to remove oxygen from iron ore.
When that carbon combines with oxygen - you get CO2; the climate-altering gas that the world is so desperately trying to reduce from human activities.
Enter HYBRIT - Hydrogen Breakthrough Ironmaking Technology - a joint project between SSAB (Svenskt Stål AB), LKAB (Loussavaara-Kiirunavaara AB), and Vattenfall.
It’s the contention of HYBRIT that instead of using carbon as a reducing agent, hydrogen can take its place. Given that when hydrogen combines with oxygen it produces water, this would eliminate the CO2 emissions associated with this part of the steel production process.
And, whilst there are a number of other projects and companies exploring hydrogen-based steel production, the HYBRIT project has actually constructed a pilot plant.
The pilot plant - which was completed in 2020 - is situated in Luleå, Sweden, and centres on what the project has called a ‘shaft furnace’.
This shaft furnace is roughly equivalent to a traditional blast furnace, but instead of coke, uses renewably-produced hydrogen.
The iron-ore pellets are added to the top of the shaft furnace, with the hydrogen introduced lower down. Once combined, what HYBRIT calls ‘direct reduction’ occurs, with the furnace reaching about fifteen hundred degrees.
Because this isn’t hot enough to melt the iron, the resulting direct reduced iron emerges from the shaft furnace in a solid form. It’s then processed in an electric arc furnace, along with a very small amount of coal. Whilst this does produce CO2, it’s a vanishingly small amount compared to the traditional steel making process.
At present, HYBRIT’s pilot plant is able to produce around one ton of steel every hour using this process.
The next step involves constructing a commercial-scale demo plant. It’ll be the job of this plant to convince steel producers world-wide of the feasibility of HYBRIT’s carbon-neutral steel production process.
It’s hoped the plant will do this by producing 1.3 million tons of steel a year by 2026.
Scale: the major barrier to carbon-neutral steel production
HYBRIT is clearly making great strides in producing steel that is as close as possible to carbon-neutral.
However, like many solutions which promise low or carbon-neutral solutions to the world’s problems, HYBRIT has run into a major issue - scale.
HYBRIT not only intends to use renewably-produced hydrogen as a reducing agent, but to power the iron ore pellet production, the electric arc furnace and the rollers which prepare the steel at the end of the process using electricity sourced from renewable sources.
In regard to the hydrogen, engineers have estimated that to produce enough green hydrogen (through electrolysis) to make a ton of steel requires 2,600 kilowatt-hours (kWh) of electricity.
To put this into context, this is not much less electricity than the average UK three-bedroom home uses in an entire year! (2,900 kWh according to British Gas).
Given that global steel production stands at just under two billion tonnes per year, HYBRIT’s hydrogen-based steel production process would require seven thousand terawatt hours (7,000 TWh) of electricity.
With global renewable energy capacity being approximately 8,300 TWh (as of 2021, per the IEA), a truly vast build out of renewable energy generation would be required to meet demand from the steel industry.
And that’s just electricity to produce the hydrogen. It doesn’t take into account the electricity to power the other parts of the production process.
Vast new hydrogen electrolysis infrastructure would also be required - far beyond that which is currently available.
Nevertheless, with all the efforts outlined above, we can be fairly certain that the carbon emissions associated with steel production will drop in the years to come - if not become entirely carbon-neutral.
The Lab: the go-to metallurgy experts
As you can tell - we like studying, analysing and talking about metal! Our team of metallurgists is able to carry out a range of materials testing and non-destructive testing services to help you identify and forensically analyse metals.
Speak to The Lab about your metallurgical requirements today
For more materials science, materials testing and inspection news and insights, explore The Lab’s News and Knowledge Hub…
Is Carbon Neutral Concrete on the Horizon? | Shell to Build Europe’s Largest Renewable Hydrogen Plant | Could Green Ammonia Replace Fossil Fuels for Shipping?
- Author
- Dr Holly Edwards
- Date
- 23/05/2023