Unravelling the mystery
For a long time, researchers knew that Roman concrete was essentially a mix of semi-liquid mortar and aggregate.
However, the aggregate used in Roman concrete tended to be made up of large chunks of stone or brick, as opposed to the very finely crushed gravel and stone used in modern concrete.
It’s for this reason that Roman concrete has a rather ‘brutal’ unfinished appearance in comparison to modern concrete.
Researchers also had a handy primary source to work from; Vitruvius’ treatise De architectura which is estimated to have been written at some point during 30-20 BCE.
In this astonishing document, Vitruvius describes how concrete walls should be at least two feet thick (or in Ancient Roman terms ‘two pedes thick’), and made from, “squared red stone or of brick or lava laid in courses”.
Despite this, the mystery remained unsolved.
However, scientists and researchers were edging closer to cracking the secret of Roman concrete.
Take Admir Masic, for example. As an environmental engineer at MIT, he had studied Roman concrete for several years. In fact, he’d even been working on new ways of analysing Roman concrete. These included the use of Raman spectroscopy for chemical profiling and multi-detector energy dispersive spectroscopy (EDS) for phase mapping samples of concrete.
Further progress
By 2021, Masic, along with several other researchers, made an interesting discovery whilst analysing concrete samples taken from the Tomb of Caecilia Metella.
By using a scanning electron microscope and the Advanced Light Source (a specialised particle accelerator that generates bright beams of x-ray light), the team discovered that the Romans added volcanic tephra to their concrete.
This tephra contained high-levels of potassium-rich leucite. Because of this, the potassium in the mortar would dissolve and effectively reconfigure the binding phase of the concrete.
Whilst the use of volcanic ash in Roman concrete had long been known - and had been assumed by many as being the reason for the concrete’s longevity - it was the identification of the leucite which was the important new discovery. This led Masic to identify another unusual feature of the concrete - ‘lime clasts’.
The breakthrough
Although traditionally regarded as being a by-product of poor mixing practices, Masic held firm to his belief that the development of lime clasts within the concrete was intended. He said:
“The idea that the presence of these lime clasts was simply attributed to low quality control always bothered me.
If the Romans put so much effort into making an outstanding construction material, following all the detailed recipes that had been optimised over the course of many centuries, why would they put so little effort into ensuring the production of a well-mixed final product? There has to be more to this story”.
It turns out there certainly was more to the story.
Using multi-scale imaging tools and chemical mapping, Masic was able to confirm that the lime clasts had formed because the Romans used ‘hot mixing’ in the production of their concrete.
But, what is hot mixing? And, how is it the secret to the longevity of Roman concrete?
Masic explains:
“The benefits of hot mixing are twofold. First, when the overall concrete is heated to high temperatures, it allows chemistries that are not possible if you only used slaked lime, producing high-temperature-associated compounds that would not otherwise form.
Second, this increased temperature significantly reduces curing and setting times since all the reactions are accelerated, allowing for much faster construction”.
But, most importantly, hot mixing - and the resulting lime clasts - impart self-healing properties upon the concrete.
The latest study conducted by Masic and the wider team at MIT found that when cracks formed within Roman concrete, they would be more likely to move through the lime clasts. These clasts are then able to react with water - which produces a calcium-saturated solution.
In turn, this solution will either recrystallise - filling said cracks - or will react with the volcanic tephra to strengthen the concrete’s composite material.
To confirm their hypothesis, the team made their own samples of Roman concrete using the methods outlined above. When deliberately cracked and subjected to water, the samples created using the hot-mixing method with lime casts healed completely within two weeks.
The Lab's Materials Laboratory Technical Lead, Holly Edwards, commented, “The most astonishing part for me, was that Romans utilised the environment, for example the rain, to form a glue that sticks the cracks back together. The mechanism for this self-healing process is incredible, resulting in there being little to no requirement for maintenance on the structures. It will be exciting to observe the progress in research towards improving the durability of concrete in general, and also 3D printed concrete formulations.”
The process for hot mixing and the self-healing process can be seen in the diagram below.
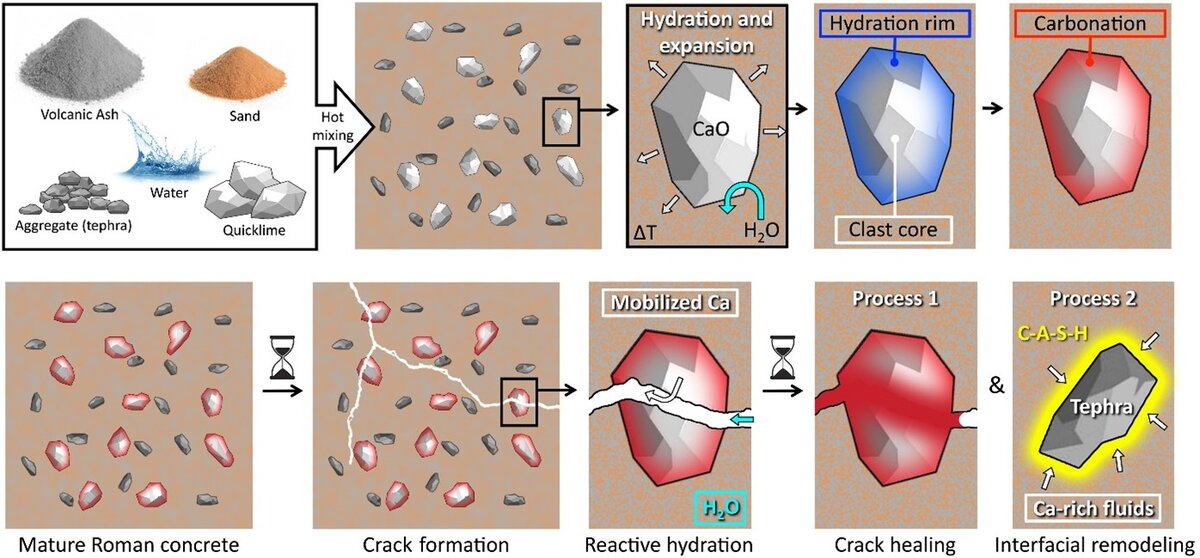
Looking forward
With the mystery of Roman concrete seemingly solved, attention has now turned to how this new-found knowledge could be used to create long-lasting concrete in today’s construction industry.
With concrete production currently accounting for approximately eight percent of total global carbon emissions, any developments that prolong the service life of concrete are to be warmly welcomed…
Materials analysis: it's more important than you think!
Thanks to the use of advanced materials analysis techniques, researchers have been able to unlock the secret of Roman concrete.
If you want to unlock the secrets of a material - then The Lab can. Our materials testing service can provide you with the answers you’re seeking - helping you to determine the true composition of a material.
Our materials science experience includes:
- Providing recommendations on metallic design and materials selection.
- Consultancy support for large-scale fabrication projects.
- Advising on quality and manufacturing disputes.
- Corrosion analysis and providing advice on corrosion management.
- Analysis of ferrous and non-ferrous metals, including rebar, steel coils, aluminium sheets/ingots, and various finished products.
So, if you require materials analysis support - The Lab is here to help.
Find out more about The Lab’s materials testing services now
For more materials science, materials testing and inspection insights and news, explore The Lab’s News and Knowledge Hub…
Researchers Discover the World’s Toughest Material | Researchers Discover Material With ‘Memory’ | Is Carbon Neutral Concrete on the Horizon?