What Metals Are Ferrous?
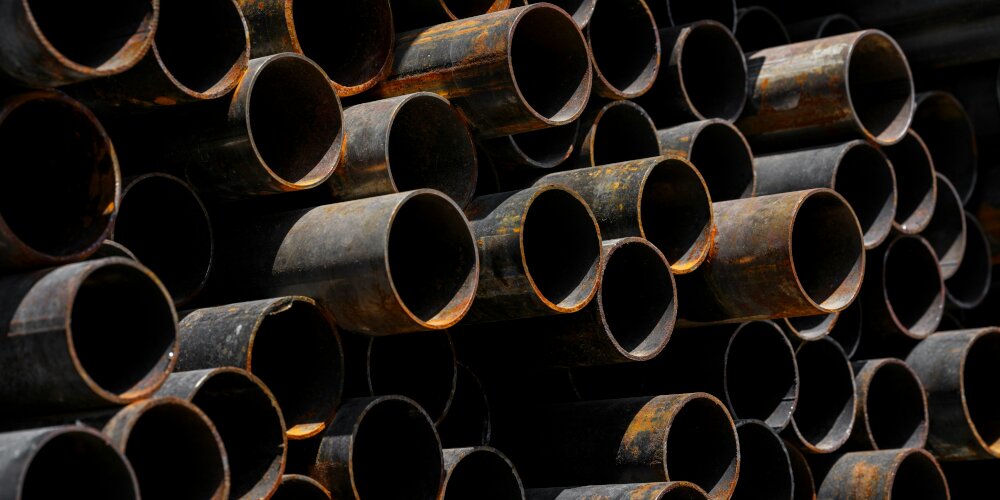
Metals have been prized for their unique characteristics for millennia, when the Stone Age ended with human metalworking. Obviously, since then techniques for refining, identifying, and utilising metals have advanced. But, one of the primary ways to distinguish metals remains – and that is whether they are ferrous or not.
But what does ferrous mean, and why is it important to know if metals are ferrous? The Lab explains answers to these questions (and more) below…
What does ferrous mean?
Ferrous means ‘containing or consisting chiefly of iron’. In fact, the root of ferrous is ferrum, which quite literally means ‘iron’ in Latin. When applied to metals then, this term is used to categorise those that contain iron in some capacity.
What are examples of ferrous metals?
Some of the most commonly used metals in construction and manufacturing are ferrous. These include:
- Non-alloy steels: these are a category of ferrous metals that have a combination of iron and carbon in varying amounts. They include:
- Low carbon steel: also known as mild steel, these are a low-carbon containing version of steel that are relatively low cost and malleable.
- Medium carbon steel: with around 0.3-0.6% carbon, medium carbon steels have an increase in strength and hardness.
- High carbon steel: increasing the carbon content up to 1%, high carbon steel is the strongest within this category, but is less ductile.
- Alloy steels: separated out from ‘non-alloy steels’ this category covers steels that have been alloyed with other metals. The most famous of which is stainless steel. This is an iron and chromium alloy, which may also contain elements such as nickel or molybdenum to enhance specific qualities. Stainless steel has improved corrosion and rust resistance, tensile strength and wear resistance.
- Other metals alloyed with steel include the following:
- Manganese: enhances strength, reduces ‘hot shortness’ (where steel gets brittle at high temperatures), and work hardening (where the steel actually gets harder and stronger under deformation).
- Nickel: improves strength, corrosion resistance, and toughness at low temperatures.
- Silicon: increases oxidation resistance at high and low temperatures, strength, electrical resistivity, and acid resistance.
- Vanadium: refines the grain structure for increased toughness, wear resistance, and sustainability.
- Molybdenum: increases strength, hardenability, in addition to creep resistance and strength at higher temperatures.
- Other metals alloyed with steel include the following:
- Cast iron: an iron alloy, containing around 2-4% carbon, and other elements in varying amounts such as silicon and manganese. Cast iron has high compressive strength and wear resistance, but is relatively brittle and prone to cracking under stress.
- Wrought iron: this largely contains pure iron, with very small amounts of ‘slag’ (a by-product of iron smelting) incorporated during the manufacturing process. Wrought iron is highly malleable, corrosion resistant, and easy to weld. It can also be re-worked, unlike cast iron.
As you can see, each of these metals have varying concentrations of iron, combined with additional materials to enhance certain characteristics. This is vital when it comes to using ferrous metals in engineering, manufacturing, and more…
What are the properties of ferrous metals?
For there to be a clear distinction between ferrous and non-ferrous metals, it corresponds that there are specific properties that help to distinguish between the two. The main characteristics that typify ferrous materials are:
- Ferromagnetic: due to their iron content, ferrous metals are magnetic (and able to be magnetised). This has made them popular within manufacturing, particularly for:
- Electronics and home appliances.
- Navigational equipment.
- Industrial machinery.
- Transportation and automotive motors.
- Density: ferrous materials are denser, meaning they are heavier. This can have an impact on their applications, as those where weight is a consideration may suit a non-ferrous alternative.
- Poor rust and corrosion resistance: in part due to the addition of carbon, as well as the inherent propensity of iron to react with external factors (like water or oxygen), ferrous metals tend to be vulnerable to rust and corrosion damage. Rust is where iron reacts with oxygen, creating iron oxide, which may weaken the structural integrity of a component. However, there are exceptions to this:
- Stainless steel: the addition of chromium creates a protective, self-healing barrier of chromium oxide to protect from further oxidation.
- Wrought iron: while this rusts eventually, wrought iron is more resistant to oxidising. The incorporated slag also helps it to resist corrosion.
- Galvanised steel: galvanising is a process that creates a type of coating made from zinc, which can help to protect the metal from water or oxygen ingress (and subsequent rusting).
- Durability: ferrous metals are known for being highly durable, which makes them valuable for long-term use in construction, urban infrastructure, and machinery.
- Tensile strength: one of the most valuable qualities of ferrous metals are their high tensile strength. Tensile strength is a measure of how much stress a material can take before fracturing or breaking – with ferrous metals consistently outperforming their non-ferrous counterparts.
- Electrical conductivity: like many metals, ferrous metals are good conductors of electricity because they have delocalised electrons which can carry the charge through the material.
- While not the best, ferrous metals are still sufficient for many applications where conductivity is required.
How to identify ferrous metals
There are several ways to identify ferrous metals depending on your needs depending on your level of expertise. Some rudimentary ways that may help to identify them include:
- Magnetism: as we mentioned above, ferrous metals are often magnetic. A quick way to tell if a metal has iron in it then, is to see if it’s attracted to a magnet.
- Visual appearance: ferrous metals are typically dull greys, black, or rusted. Checking on the visual appearance (particularly whether a component has rusted or not) may be a way to tell if a metal contains iron.
- Weight: ferrous metals are typically heavier than other alternatives. As such, using a weight comparison may help you to identify if your metal falls into this category.
- Metal detectors: metal detectors emit an electromagnetic field to identify metals. Ferrous metals exhibit a lower Target ID value based on their conductivity and magnetism.
However, if you want to be certain, the best way to identify ferrous metals is through scientific testing. Methods for this include:
- Chemical composition: using Positive Material Identification (PMI) methods, like Optical Emission Spectroscopy (OES), you can determine the exact chemical composition of a metal, including the presence of iron.
- Hardness testing: while not definitive on its own, using hardness tests (such as Vickers) can assist with identifying ferrous metals. This is because they are typically harder than non-ferrous metals.
Why is it important to know if metals are ferrous?
Now that you have a grounding in the properties of ferrous metals, it’s time to look at just why this knowledge is important.
Application
Whether you are an engineer, materials scientist, or work in manufacturing and design, the primary reason you need to know about a material is to make sure you’re using it for the correct application. As we explained above, ferrous metals have specific properties that will make them more or less suited to different uses.
For example, different types of steel are in incredibly high demand, for everything from ship-building and construction, to medical and electrical equipment. This is because they have excellent strength and durability. However, weight and relatively poor corrosion resistance may prohibit from being used in places where these are important considerations; such as:
- Lightweight applications like aerospace engineering or portable machinery.
- Humid or corrosive environments.
Alongside using the correct metal for the job, understanding if a metal is ferrous means you can use the optimal material for a job. For example, you wouldn’t use ferrous metals for certain applications like electronic wiring, even though they are capable of conducting electricity – because they are not the best at it.
Disposal and recycling
Knowing the composition of your metal, such as if it is ferrous or not, is essential for disposal when your components reach the natural end of their usability. This is because different metals require certain treatments for recycling or disposal.
Ferrous metals are recyclable, but it is not as easy as it is for their non-ferrous counterparts. They must be carefully separated from other metals before being processed, melted down, and purified. Fortunately, while this can be a labour-intensive process, the quality doesn’t degrade – meaning you can get reusable, high-quality metals back for a fraction of the energy required to extract the virgin metal from ores.
Cost
Ferrous metals are relatively inexpensive (in comparison to non-ferrous metals at least) which is part of the reason they are so popular in construction and engineering. Iron itself is relatively common, and the ability to recycle ferrous metals is vital for sustaining their usability. When it comes to component design or experimentation, it may be more cost-effective to use a ferrous metal if it meets the demands of the application.
Rust susceptibility
Lastly, knowing if a metal is ferrous allows you to consider the rust or corrosion susceptibility during the design phases. For example, if you know your component needs to be submerged in water, or in corrosive or highlight oxygenated environments, it pays to know if your material has iron in it. Alternatively, if you know that these external factors will be relatively low, you can capitalise on the valuable characteristics of ferrous metals.
Another benefit to knowing if your metal is ferrous comes in worst-case scenarios – such as material failure or degradation. Understanding the composition can help experts to identify why a failure has happened and help to prevent it in the future.
Material identification and analysis with The Lab
Understanding material composition – such as whether a metal is ferrous or not – is essential for many industries. From engineering innovations, to manufacturing, you need to know what you’re working with to ensure you’re meeting individual standards and quality assurance. And, in a worst case scenario, knowing what your material is made of can help you to understand what went wrong during a component failure.
At The Lab, we have cutting edge technology used and maintained by experts to give you the answers you need. Contact us today for an obligation-free consultation to find out how our material testing and identification services can assist you.
Discover chemical and mechanical material identification services today
For more information and the latest industry insights, explore The Lab’s News and Knowledge Hub…
Cutting-Edge Techniques Revolutionise Metal Corrosion Analysis | MPI-SusMat Scientists Revolutionise Alloy Production With Eco-Friendly Method | Tata Steel UK and JCB Forge Groundbreaking Low-Carbon Partnership
- Date
- 23/05/2025