New Method Turns Red Mud into Green Steel
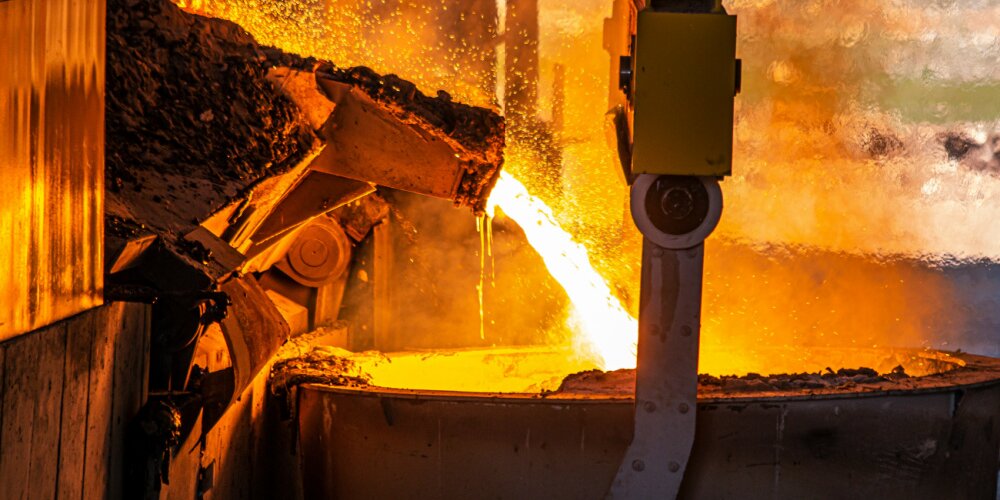
With the demand for steel and aluminium forecast to rise almost 40% by 2030, there’s been a huge push to make production more sustainable and environmentally-friendly. One of these promising reveals comes from researchers from the Max-Planck Institut für Eisenforschung in Germany, who may have a solution that uses hydrogen to convert waste from aluminium production into green steel.
During aluminium manufacture, huge quantities of bauxite residue are produced, which is more commonly known as red mud. Unfortunately, bauxite is actually highly toxic due to a combination of factors, including a high pH (or alkalinity), increased electrical conductivity, and positively charged sodium and aluminium ions.
However, there is an interesting crossover that may make aluminium and steel production work together. And it’s all because of iron. Firstly, the eponymous colouring of bauxite residue, or red mud, is due to the high concentration of iron oxide – which could be as high as 60% of the total composition. And, rather conveniently, iron is the primary metal component required for steel manufacture.
By melting red mud in an electric arc furnace, alongside a plasma containing 10% hydrogen, the scientists were able to create liquid iron that could be easily extracted in as little as 10 minutes. Even more importantly, the scientists discovered that the iron produced by this method was so pure it could be processed directly into steel. Plus, the additional and newly non-corrosive metal oxides from the bauxite residue cool into solid form, which can then be converted into a glass-like material and reused in the construction industry.
According to Matic Jovičević-Klug, the study’s lead author, their new process could “simultaneously solve the waste problem of aluminium production and improve the steel industry’s carbon footprint”.
Considering that the aluminium industry produces an average of just under 200 million tons of bauxite residue per year, and has high processing costs around disposal, finding a solution to reuse this material is not only economically sensible, but environmentally necessary. Combining this with green steel production can help to reduce the environmental impact of both of these valuable materials in the future.
The team’s plasma reduction method has also been designed to reduce the economic burden on the metals industry. Electric arc furnaces are commonly used already, so it would require limited adjustments and investments for the industry to become more sustainable using this method.
With the two-for-one benefits of this method, and the relatively low levels of iron oxide required for economic viability, co-author Dierk Raabe is right in saying that it’s now “up to the industry to decide whether it will utilise the plasma reduction of red mud to iron”.
Looking for materials testing excellence?
Then you’ve come to the right place. At The Lab, we have a superb team of professionally-trained experts who can conduct a wide range of tests and analyses to help you understand more about the materials you work with.
Using premier techniques like advanced digital microscopy, our team can find the answers you need.
Contact The Lab today for a consultation
For more industry insights, news, and information, explore The Lab’s News and Knowledge Hub…
Scientists Recycle Cigarette Butts to Assist With Biodiesel Production | Researchers Observe 'Self-Healing' Metals | Researchers Find an Innovative New Use For Plastic Waste
- Author
- Adam Whittle
- Date
- 03/05/2024