New laboratory services grow despite pandemic
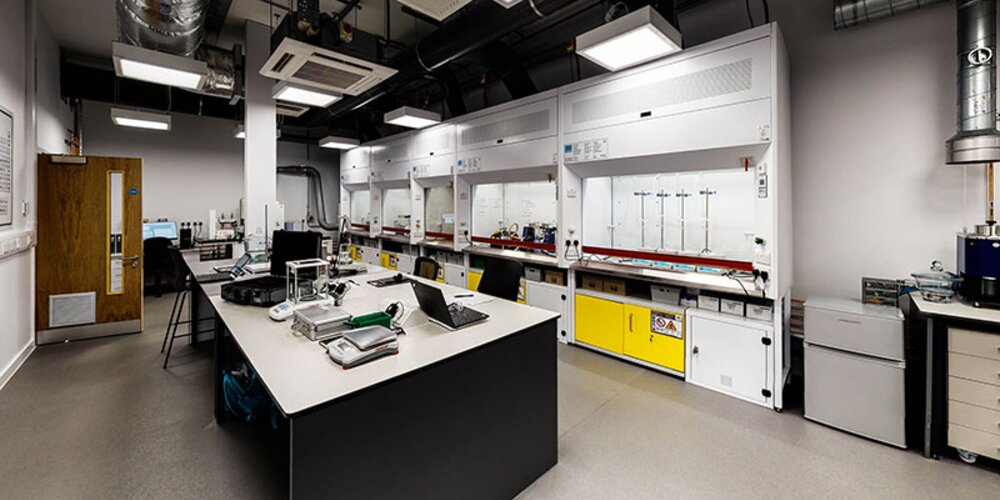
Brookes Bell opened its new Laboratory and Technology Centre at the end of January providing a home for its new metallurgy, fuel testing and non-destructive testing services. Matthew Calveley, Laboratory Manager and Technical Lead for Metallurgical Services at the Lab, talks about the first three months and the team’s work so far.
The 8,000sq ft facility is in Bidston, Wirral, nr Liverpool in the UK and is home to innovative testing and inspection facilities, including a modern laboratory, an engineering workshop space, flexible training facilities and offices.
“To progress this idea from a paper proposal to actual bricks and mortar reality is one thing, to open and grow our services in the midst of a global pandemic and national lockdowns is another challenge in itself” says Matthew Calveley, “but I’m really pleased with the progress we’ve made. Our core metallurgy work has continued steadily, the work to achieve ISO accreditation for our fuel services is progressing well and our new specialisms – including fuel and paint coatings analysis are continuing to grow. It’s a very positive start.”
The laboratory officially opened in January and because of the need to be near the specialist equipment for carrying out testing, the teams have been working from the new unit ever since. There have been some limited opportunities for the NDT team to travel for site work, in both Scotland and Gibraltar, utilising their specialist equipment which has been encouraging.
More recently, the laboratory has also begun to welcome clients and visitors from across the UK for the purpose of witnessed investigations. It’s been great to show off the facility and the feedback has been overwhelmingly positive says Matthew.
The laboratory has adjusted to the requirements of social distancing, with staff and customers separated and using masks. Hand sanitiser stations, routine cleaning and proximity sensors have been used to ensure a safe environment. In the microscopy suite, each inspection unit has a large wall mounted screen, which has allowed images to be reviewed easily by groups of socially distanced observers. Brookes Bell have also put in place contingency plans which allows customers to dial in from another location to witness testing if needed.
One development that Matthew welcomes is the sheer diversity of work coming in. One of the goals of the new laboratory was to widen the organisation’s services and expertise to cover other industry sectors, and this is already happening.
The laboratory is securing industrial land-based work, in addition to the core maritime work. For example, the metallurgy team have been looking into a train engine failure, investigating the fractures and working to identify the mechanism of failure to help the client with their wider root cause analysis process.
Discussing the new business areas, Matthew says: “We’ve been doing more coatings analysis inspections than we expected. The microscopes weren’t bought expressly for this kind of work, but their flexibility of use is proving invaluable. In recent years coatings have become increasingly complex and as a result, the equipment used to examine them needs to be capable of deconstructing and investigating this complexity. There are very few other companies in the world that can offer the level of paint flake analysis that we can, and with our capability and expertise, the opportunities for growth are exciting.”
Another area for growth and innovation within our services is superyachts. The construction of these vessels utilises some complex and cutting-edge materials which are usually very high value, any damage claims are correspondingly high too. Our combination of modern inspection techniques and high-quality expertise make us unique in that sector and It’s exceptionally complex and interesting work too, adds Matthew.
Meanwhile the fuel team continue to alternate between investigations and analysis and working to achieve the new laboratory’s industry accreditations, including the ISO 17025 standard. This involves compiling all the management procedures and assembling the supporting data and information. The goal is to attain ISO status by the end of the year, which would be a huge achievement, but the timing may be determined by the backlog of work facing the ISO accreditors because of the pandemic.
The fuel testing services team have been analysing fuel samples in accordance with table 2 of ISO 8217, checking for substandard samples and identifying the causes and origins of any fuel-related problems. The laboratory’s new high-end advanced analytical equipment is also allowing the team to provide a more detailed analysis than table 2 of ISO 8217 where it’s required
In the months ahead, Matthew is looking forward to the increase in opportunities and welcoming some of the forensic engineering and analysis work that’s been more challenging to attract with the global pandemic travel restrictions and lockdowns in place. In addition, the laboratory team is keen on engaging with local businesses and inviting industry professionals to visit for demonstrations and really showcasing the breadth of capabilities of the new laboratory.
- Author
- Matthew Calveley
- Date
- 28/04/2021