NASA Harnesses AI to Drastically Reduce Product Development Time
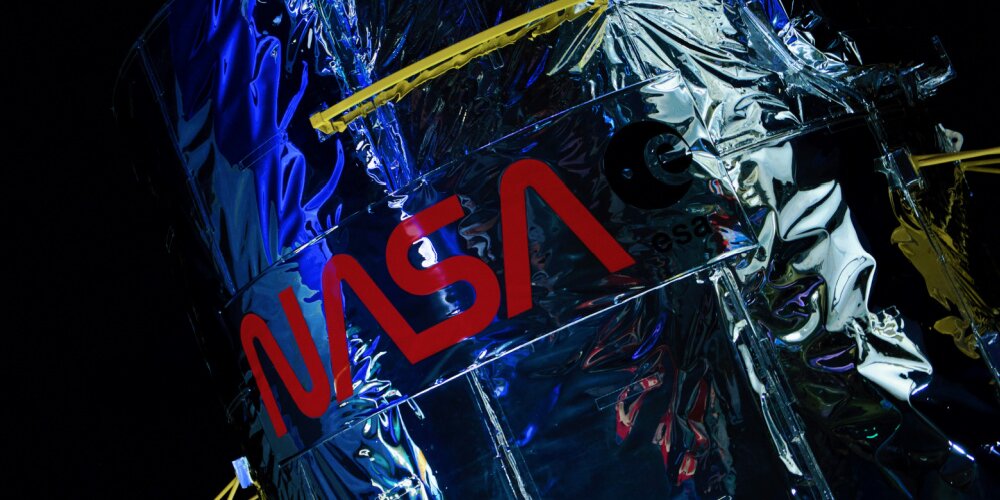
NASA has demonstrated the potential of generative design and advanced digital manufacturing technologies provided by Protolabs, slashing the development time for space components from years down to just 36 hours.
The U.S. government organisation has been leveraging artificial intelligence to produce computer-aided design (CAD) models that meet its stringent requirements for space missions.
This incredible approach was showcased during the PowerSource Global Summit, where participants collaborated to outline the specifications for a generatively designed part. The objective was to create a holder for a flask that captures volatile gases released when the moon's surface warms up.
The project is part of NASA's ambitious Artemis mission, which intends to explore the feasibility of establishing permanent human settlements on the moon and Mars.
The designed component needed to meet several critical criteria: it must support up to 68 pounds of weight, endure temperatures as low as -193 °C, fit within a shoebox-sized volume, and be stackable to minimize space usage on the spacecraft. Additionally, it had to be adaptable to various ground conditions, including sloped surfaces.
Weight considerations are extremely important for space missions, with NASA estimating the cost of launching each kilogram into space at approximately $1 million. To meet the project's tight schedule constraints, the chosen manufacturing method had to allow for rapid production, ruling out metal 3D printing.
Engineers opt for aluminium 6061, a precipitation-hardened alloy known for its excellent strength-to-weight ratio and stress tolerance. With these specifications in hand, AI generated the optimal CAD file for CNC (computer numerical control) machining.
The manufacturing process then moved through tool pathing, ending in 19 hours of milling and 4 hours of processing.
Protolabs' Manufacturing Engineer Manager for CNC Machining, Greg Perz, stated: “While AI speeds up the process you can’t underestimate the human element to ensure that there were no alarms or errors in the milling process”.
The generatively designed component featured breaks in its circular design, which significantly reduced milling time by enabling simpler two-axis machining. This not only saved hours but also showed the efficiency of combining AI-driven design with expert human intervention.
Mechanical Engineer at NASA's Goddard Space Flight Center, Matthew Vaerwyck, reflected on the project's outcomes: “We didn’t know what we were going to make in the end. What they got was between six to ten times improvement in mass, stiffness, and design time”.
This approach may prove the key to unlocking the potential for permanent inhabitation on the moon and Mars. As NASA continues to work towards its ultimate goal, it will be interesting to see how AI continues to revolutionise possibilities.
Scanning electron microscopy at The Lab
Microscopy is a crucial part of modern failure investigations and forensic analysis.
At The Lab, our Scanning Electron Microscope (SEM) is designed for flexible and complicated scopes of inspection and can cater for a broad range of different sample types, across a wide range of magnifications and inspection techniques.
To find out more about The Lab’s scanning electron microscopy capabilities today, get in touch with our team.
Learn more about our SEM services at The Lab
For more information, industry insights, and the latest news, explore The Lab’s News and Knowledge Hub…
Princeton University Engineers Tough Concrete Inspired by Human Bone | Scientists Test UV Glass to Disrupt Biofilm Formation in Water | Reusable 3D-Printed Glass Bricks Could Cut Construction Emissions
- Author
- Anthony York
- Date
- 17/02/2025