MPI-SusMat Scientists Revolutionise Alloy Production With Eco-Friendly Method
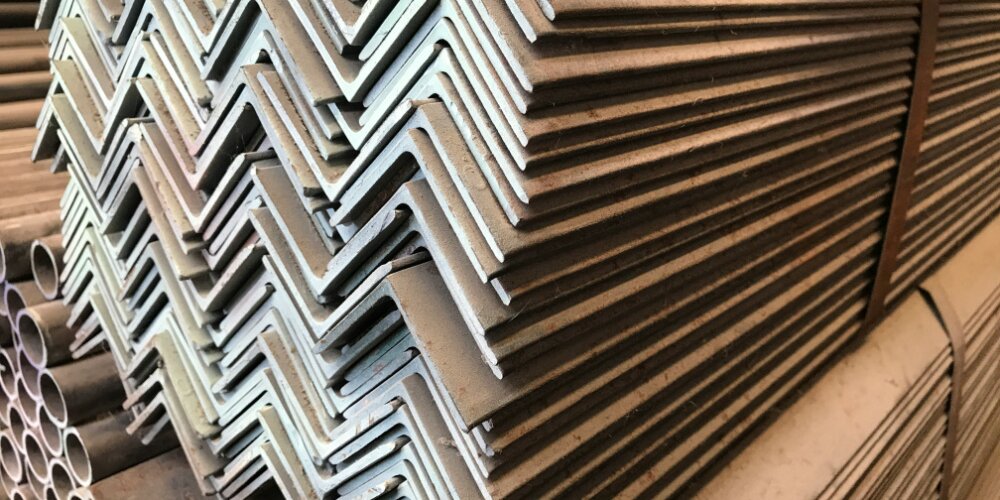
Scientists at the Max Planck Institute for Sustainable Materials (MPI-SusMat) have designed a process that merges metal extraction, alloying, and processing into a single, environmentally-friendly step.
The existing method of producing alloys is an energy-intensive process, which involves the extraction of metals from their ores, alloying, and extensive thermomechanical processing. These metals form the foundation of alloys that have a low thermal expansion, called Invar.
Each step in this process consumes considerable amounts of energy, and contributes heavily to greenhouse gas emissions.
The production of metal is responsible for 10% of Global carbon dioxide emissions. Iron production alone contributes 2 tons of CO2 for every ton of metal produced, and Nickel production emits 14 tons of carbon dioxide per ton produced.
"We asked ourselves: can we produce an alloy with near-optimized microstructure-property combination directly from ores or oxides with zero CO2 emission?" said Dr. Shaolou Wei, Humboldt research fellow at MPI-SusMat and first author of the publication.
The method simplifies and streamlines the production of Invar alloys. By combining the process of metal extraction, alloying, and thermomechanical processing into one step within one reactor, it eliminates the need for multiple steps, and significantly reduces the overall energy requirement.
"The key idea is to understand the thermodynamics and kinetics of each element and use oxides with similar reducibility and mixability at around 700°C," Dr. Wei added. "This temperature is far below the bulk melting point, which still allows us to extract metals from their oxide states and mix into alloys via one single solid-state process step without reheating."
One notable aspect of this revolutionary process, is the use of hydrogen instead of carbon, as a reducing agent. When used in the reducing process, hydrogen produces water as a by-product, thus eliminating CO2 emissions.
Not only does this make the process more environmentally friendly, but also enhances the quality of the resulting alloys by avoiding carbon contamination. Alloys produced with this technique not only match the low thermal expansion properties of Invar alloys, but the refined grain size, naturally inherited from the process, offers superior mechanical strength.
The new approach has the potential to transform industries that rely heavily on these materials, such as aerospace, cryogenic transport, energy and precision instrument sectors.
The team is beginning to look ahead to other applications. As iron, nickel, copper, and cobalt can all be processed in this way, questions naturally turn to whether high-entropy alloys could see the same treatment.
Another promising avenue is the use of metallurgical waste, instead of pure oxide. Removing impurities from waste materials could transform industrial by-products into valuable feedstock, further enhancing the sustainability of metal production.
Differential Scanning Calorimetry (DSC) services at The Lab
The Lab at Brookes Bell can help identify the physical and thermal properties of a range of materials including polymers, metals and amorphous materials using variations in temperature against time to monitor changes in physical properties of the sample.
Contact The Lab to find out how our DSC service can help your business.
Discover Differential Scanning Calorimetry at The Lab
For more information, industry insights, and the latest news, explore The Lab’s News and Knowledge Hub…
Researchers Create Renewable Electricity Source Using Algae | Scientists Test UV Glass to Disrupt Biofilm Formation in Water | Could Eggshells Be the Solution for Greener Rare Earth Element Recovery?
- Date
- 12/12/2024