Modern Tungsten Electrodes Improve TIG Welding Safety and Performance
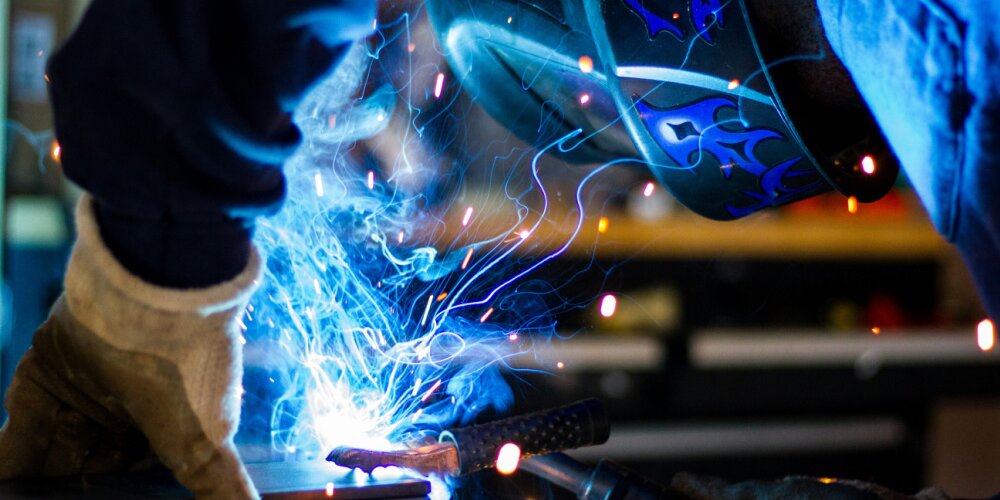
Modern tungsten electrodes provide safe and effective alternatives to thoriated tungsten, improving the performance of TIG welding without the associated health risks.
Gas tungsten arc welding (GTAW), commonly known as TIG welding, relies on tungsten electrodes for its precision and effectiveness. Historically, thoriated tungsten, produced by adding thorium oxide to pure tungsten, was widely used for materials such as stainless steel, carbon steel, copper, and titanium.
Thoriated tungsten's popularity was due to its stable arc, which is crucial for precision welding. It also minimised the likelihood of arc wandering, resulting in better control over the weld.
Additionally, it performed well at lower amperages for welding thin materials and had high resistance to contamination and wear. Thoriated tungsten could handle high current levels without significant degradation, making it a popular choice for heavy-duty welding.
However, thoriated tungsten is no longer recommended due to safety concerns stemming from the radioactivity of thorium. Today, it is primarily used only in long-standing welding procedure specification (WPS) documents across specific industries and applications.
In light of these health concerns, eyes have turned to modern alloyed tungsten electrodes, which provide effective and safe alternatives to thoriated tungsten, without the associated health risks.
Ceriated tungsten, identified by a grey band, contains 2% cerium oxide and is an excellent all-purpose electrode for both AC and DC TIG welding on materials like steel, stainless steel, and aluminium.
It provides similar performance to thoriated tungsten, with easy arc starting and good arc stability, particularly at lower amperages, which makes it ideal for welding thin materials or tasks requiring fine control with minimal heat input.
Lanthanated tungsten, available in 1.5% or 2% formulations and marked by gold or blue bands, perform well in both AC and DC welding. Its stable arc performance makes it particularly suitable for welding aluminium in AC.
It provides a very stable arc, especially at low and medium amperages, and produces consistent welds, and can carry higher current loads without overheating or losing its shape.
Zirconiated tungsten, marked by a white band and containing 0.8% to 1% zirconium, has a smooth, stable arc that is ideal for welding aluminium alloys and magnesium.
While preferred for AC welding, it is not recommended for DC welding due to its inability to maintain a stable arc at the polarity of the current and its lower current-carrying capacity.
Today's tungsten alloys meet, if not exceed, performance expectations. Modern ceriated, lanthanated, and zirconiated tungsten electrodes are more than capable of taking on any TIG task, offering safe and effective alternatives to thoriated tungsten.
Non-destructive testing with The Lab
State-of-the-art metallurgical survey, inspection, and non-destructive testing services are offered by The Lab at Brookes Bell.
Our comprehensive services include visual testing, magnetic particle testing, ultrasonic testing, eddy current array testing, and more.
To learn more about our non-destructive testing, please contact us today.
Learn about non-destructive testing services from The Lab
For more information, industry insights, and the latest news, explore The Lab’s News and Knowledge Hub…
New Ammonia Conversion Marks Leap Forward for Green Hydrogen Energy | Princeton University Engineers Tough Concrete Inspired by Human Bone | Reusable 3D-Printed Glass Bricks Could Cut Construction Emissions
- Author
- Adam Whittle
- Date
- 25/02/2025