Innovative Approach to Detecting Interfacial Debonding in Rocket Motors
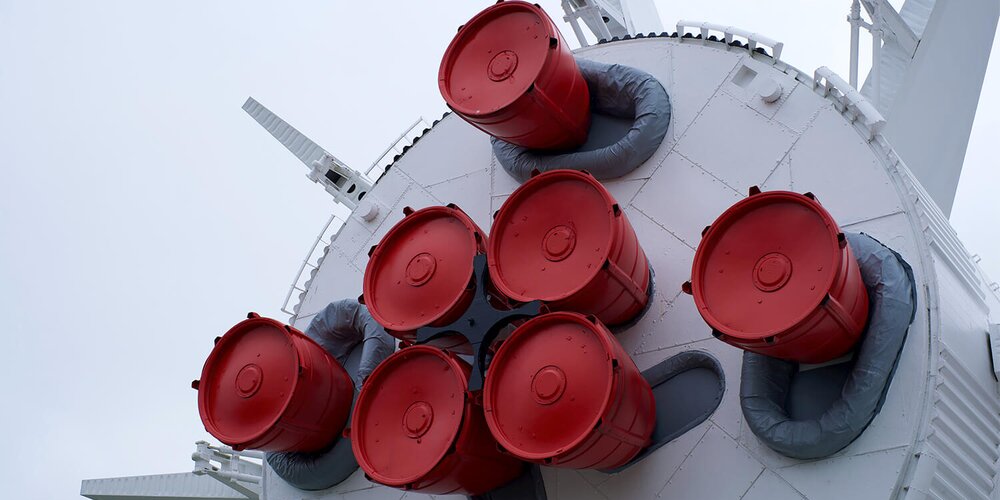
Carbon fibre-reinforced polymers (CFRPs) are widely used in solid rocket motor casings due to their exceptional performance. However, interfacial debonding between CFRP and viscoelastic materials like rubber is a significant concern.
Researchers at the State Key Laboratory of Electronic Test Technology, North University of China have developed a new method to detect interfacial debonding defects in solid rocket motors, offering a promising solution to a longstanding challenge in aerospace engineering.
The new approach utilises active Lamb wave energy analysis and introduces the Damage Evolution Factor (DEF) to detect and evaluate debonding defects in CFRP-rubber bonded structures during service and storage.
Solid rocket motors (SRMs) are essential components in aerospace and missile systems, valued for their high thrust, reliability, and ease of maintenance. To improve performance, traditional metallic materials in SRM casings have been increasingly replaced with CFRP composites.
However, SRMs are exposed to various environmental loads during service and storage, leading to potential interfacial debonding between the propellant, liner, insulation, and shell. This can result in severe consequences such as burning instability, thrust loss, and catastrophic structural failure, significantly impacting mission success and safety.
Current non-destructive testing (NDT) methods, including X-ray imaging, infrared thermography, and ultrasonic testing, have shown limitations in detecting structural damages in SRMs under operational conditions.
X-ray imaging requires complex equipment and safety precautions, making it impractical for field inspections. Infrared thermography is limited in detecting deep-seated flaws in multilayer composites. While ultrasonic guided wave methods offer some advantages, they also face challenges in detecting complex structural defects.
The innovative method proposed by researchers employs Lamb waves, which are highly sensitive to changes in material properties and can travel long distances within complex structures. Unlike traditional methods, Lamb wave-based techniques do not require complex equipment or disassembly, reducing time and safety concerns for field inspections.
Recent research has demonstrated significant progress in using Lamb waves for detecting interfacial debonding damage. Studies have shown the effectiveness of Lamb waves in identifying debonding defects in various bonded structures, including CFRP-concrete interfaces and composite laminates.
Building on this work, the researchers introduced the Damage Evolution Factor (DEF) to quantify debonding damage in CFRP-rubber bonded structures within SRMs. The detection method involves exciting Lamb waves on the surface of the structure and analysing displacement time-history response signals at observation points.
The A0 mode Lamb wave - sensitive to interfacial damage - is used as the incident wave. Displacement time-history response signals are extracted, and DEF values are calculated to quantify the debonding damage.
Numerical simulations and experimental validation were conducted to assess the method's effectiveness. The results showed that DEF values increased with the size of the interfacial debonding damage, demonstrating the method's potential for quantitative evaluation of debonding defects.
Physical experiments were also performed using CFRP-rubber sheet specimens to replicate the simulation model, and the results were consistent with the simulations.
The study confirmed the feasibility of detecting interfacial debonding defects using Lamb wave debonding energy loss. Both numerical and experimental data showed that DEF increased with the extent of damage, validating the method's effectiveness.
However, some discrepancies were noted, attributed to factors such as irregular boundaries in the test specimens and energy leakage into the bonding layer.
Future research will focus on refining the DEF metric to address uncertainties in material parameters and enhance the quantitative assessment of debonding damage. Advanced signal processing techniques could further improve detection accuracy and robustness in complex bonded structures.
This breakthrough offers a promising approach for detecting and evaluating interfacial debonding defects in CFRP-rubber bonded structures, and has significant implications for the structural integrity and reliability of solid rocket motors during service and storage.
Non-destructive testing services at The Lab
The Lab brings together the world’s finest state-of-the-art equipment and technologies with highly-experienced experts to provide the very best inspection and testing services in the industry.
Our services cover visual testing (CSWIP), magnetic particle testing (MT), phased array ultrasonic testing (PAUT), and much more.
Our highly-trained experts, using bespoke technology and proprietary software are well-versed in identifying anomalies, analysing the results and providing you with the information required to help identify issues before they happen, saving costs and time in repairs and downtime.
To learn more about our non-destructive testing services, please get in touch.
Learn more about our non-destructive testing services at The Lab
For more information, industry insights, and the latest news, explore The Lab’s News and Knowledge Hub…
Researchers Find New Way to Weld Metal Foam Without Compromising the Material | MPI-SusMat Scientists Revolutionise Alloy Production With Eco-Friendly Method | New Efficient Battery Fuel Could Revolutionise Energy Storag
- Author
- Andrew Yarwood
- Date
- 20/02/2025