Going for gold
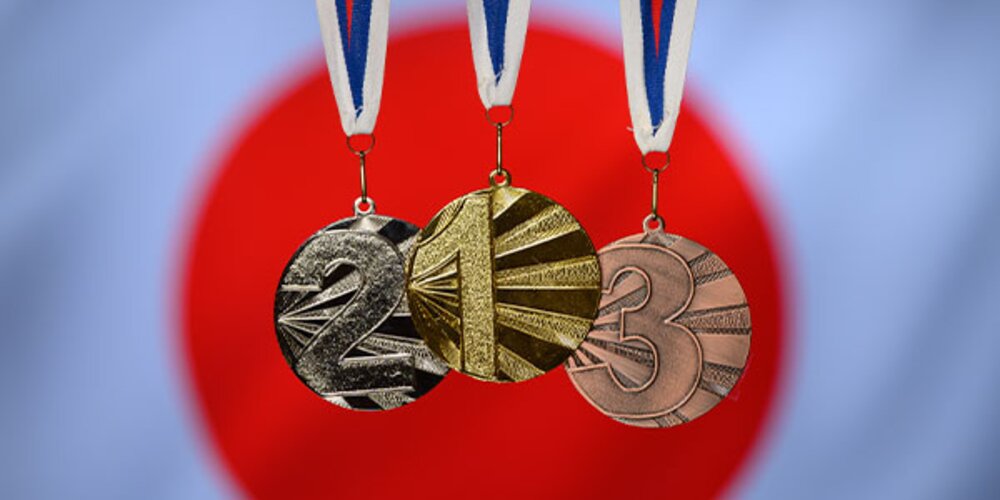
Going for gold
Metallurgy is a branch of science and engineering, involving the study of metals and materials. By understanding the fundamental behaviour of metals, Brookes Bell’s metallurgists can determine how a component or structure should react in a given environment or under certain mechanical loads.
Matthew Calveley, Brookes Bell’s laboratory manager and senior metallurgist has been reflecting on the precious metals presented to athletes competing in the Tokyo 2020 Olympics and Paralympics.
As everyone knows medals of gold, silver and bronze are given to the top three places in each event. This has not always been the case. In the ancient Olympic Games the winner was given an olive wreath, while the first modern Olympic Games (1896) saw the winners presented with silver for first place and the runners up were given a copper or bronze medal.
The gold, silver and bronze sequence first began in 1904. What's quite interesting about this sequence is these are all group 11 elements in the periodic table - so they all share some similar characteristics such as being relatively inert and all have good electrical conductivity. It's probably their inert properties that make them aesthetically pleasing as medals, and why they were some of the first metals discovered and given value.
The composition of the medals given to athletes does vary from games to games. The gold medal this year (Tokyo 2020, held in 2021 because of the pandemic) is silver plated with gold, the silver medal is pure silver and the bronze medal is actually red brass (so it's not actually a bronze medal!).
Gold medal
Pure gold is a very soft and ductile metal, such that it can be hammered into very thin sheets. Before chemical analysis was possible, the purity of gold could have been assessed by biting it to see if it became indented (enamel is harder than pure gold and this may be where the biting of gold medals originates). Therefore, maybe biting gold could be considered one of the earliest forms of material testing!
Although the original value of gold comes from its nobility and seemingly everlasting lustre – in its pure form it wouldn’t be very durable as jewellery. For this reason (but mostly for cost reasons) small additions of other cheaper metals are added to gold jewellery to improve its strength and durability. This could either be small additions of silver to make a white gold or copper to make a redder type of gold.
Pure metals can still have very useful properties of their own, such as high conductivity of heat and electricity, but they don’t tend to have very good mechanical characteristics – which means they don’t lend themselves readily to structural engineering applications or situations where durability is required.
When two (or more) different metals are blended together, it is possible to create a new metal substance which could have some similarities with its parents or it could take on a unique personality with its own set of properties. This process is called alloying and it is the most important way in which the strength of metals can be improved. Alloys tend to be stronger than pure metals.
This strengthening is based on the atoms of one metal having a different size and chemistry to the other and, without going into too much information on dislocation movement and the movement of atoms within the crystal structure of metals, the presence of one type of atom restricts the ease of movement of the other atoms while the structure is under load.
One of the earliest metals ever discovered by our ancestors, copper, was improved through the creation of bronze (which is an alloy of copper and tin. The current Olympic and Paralympic medals are brass, which is a mixture of copper and zinc). This discovery ushered in an era of human progress which included improvements to tools and weapons - making them stronger, more durable and more easily worked.
Silver medal
So, you've just finished second and been awarded a silver medal - how would you make sure the medal was real silver? You could analyse it using a range of quick laboratory techniques (using XRF – X-ray fluorescence, OES – Optical Emission Spectroscopy, or LIBS – Laser Induced Breakdown Spectroscopy) or you could use a cube of ice?
Silver has a high thermal conductivity - higher than copper and gold (all group 11 elements in the periodic table). In contact with ice, it melts the ice quickly and at the same time the metal itself is cooled rapidly by the ice too. Try it next time you have something you believe to be pure silver – although ideally, it would be best viewed in comparison with other known metals to compare the rates of melting.
Bronze medal
Bronze and brass are both alloys of copper (basically a mixture of metals), but they both contain different alloying elements (tin with copper for bronze and zinc with copper for brass). As highlighted earlier, the current Olympic and Paralympic medals are brass. We can only assume there is something about the appearance or processing of red brass that makes it more suitable than bronze.
Bronze has many uses including marine applications such as bushings, bearings and propellers because of its resistance to corrosion in seawater. It also has good metal to metal friction properties and good conductivity for electronics applications. Copper based materials have anti-bacterial properties too. All very useful things.
Fun facts
This years’ Olympics all the medals have been manufactured from recycled electronics products - from 80 tons of equipment (sourced in Japan over two years), 70 pounds of gold, 7700 pounds of silver and 4850 pounds of bronze.
and last but not least … based on their value as a commodity the gold is worth $790, the silver is worth $440 and the bronze is worth just $4!
Failed attempts
But what about those who don’t win? Even for those that succeed, failure was likely part of the process. Understanding what went wrong provides good information on how to prevent it from happening again.
The failure analysis of metal components in engineering processes is a core part of our work - getting broken bits and pieces and understanding how and why they failed. We will analyse and assess the materials involved, understand the design, its environment and the history of the component, but a successful analysis that allows us to understand and learn from a failure can prevent it from happening again and more importantly can improve safety and reliability going forward.
Our thanks to Matthew for letting us use this article which is edited from several original posts on his Linkedin page: https://www.linkedin.com/in/matthew-calveley-7b050730/
- Date
- 07/09/2021