Cutting-Edge Techniques Revolutionise Metal Corrosion Analysis
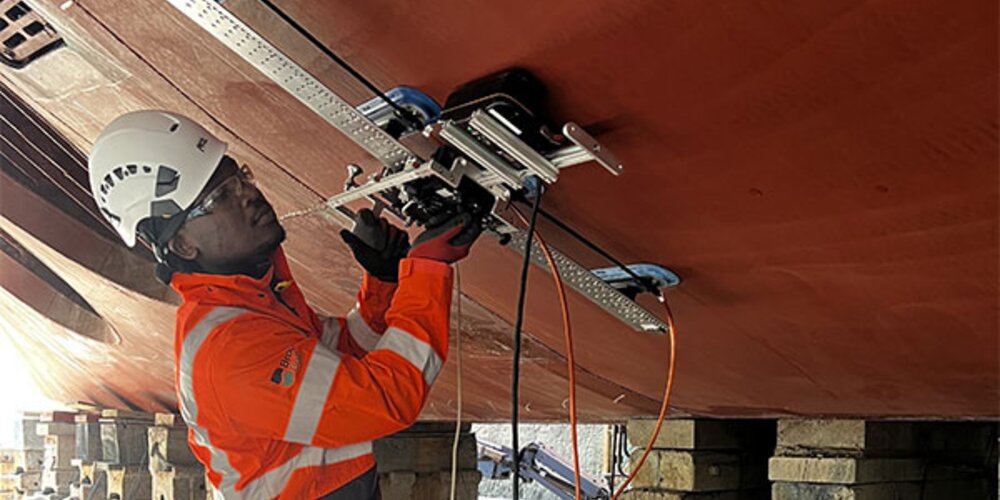
Researchers at the Pacific Northwest National Laboratory (PNNL) have developed innovative methods to monitor and understand metal corrosion, providing unprecedented insights into how and why this destructive process occurs.
One of the primary obstacles in corrosion research has been the reliance on traditional “cook-and-look” methods, explained Vineet Joshi, materials scientist at PNNL.
“Typically, researchers take a sample, immerse it in their chosen medium and, after a certain period of time, observe the corrosion—but only after it has occurred. Then, they generate numerous hypotheses to explain the corrosion,” Joshi added.
This approach has significant drawbacks, as it only provides snapshots of the corrosion process, leading to speculation about its progression and potentially skewed results from repeated sample handling.
Alternative methods - such as the scanning vibratory electrode technique or scanning electrochemical cell microscopy - attempt to measure electrochemical properties inside the samples. However, surface abnormalities and irregularities can interfere with these techniques, compromising the accuracy of the results.
Recognising the limitations of existing methods, PNNL researchers embarked on developing a more precise approach to monitor corrosion in real time.
Their solution, known as multimodal corrosion analysis, combines sensors, cameras, electrodes, and a hydrogen collection tube to observe the progress of corrosion in simple atmospheres, understand surface properties using electrochemical techniques, and collect hydrogen gases - a by-product of corrosion.
“By combining data from these simple and diverse modalities in real time, we can address fundamental questions regarding how corrosion initiates and propagates in materials,” explained Sridhar Niverty, materials scientist at PNNL.
“The correlative imaging aspect also informs us about where to further investigate our materials to learn about why they corrode. The synergistic combination of these techniques yields significantly more information about a material's performance than was possible until now”.
PNNL scientists developed scanning electrochemical cell impedance microscopy to further enhance the precision of corrosion analysis. By focusing on localised and time-dependent electrochemical properties without interference from nearby regions, researchers can identify weak and strong spots on the surface prone to corrosion.
“In this technique, we have everything needed to initiate the corrosion in a very small tube—or pulled capillary—including the electrolyte, reference, and current-collecting electrode,” said Venkateshkumar Prabhakaran, chemical engineer at PNNL.
“By landing the tiny opening of this capillary on the surface, we measure localized and time-dependent electrochemical properties without getting any interference from nearby regions. That helps us capture weak and strong spots on the surface prone to corrosion, which are otherwise lost when doing the bulk-scale measurement and formulate-suitable mitigation strategies”.
These advancements have significant real-world applications, particularly in developing lightweight materials and joints for vehicles. The friction stir scribe process, for example, joins materials with drastically different melting points without fasteners.
Understanding how this method affects corrosion at the interface between metals is crucial for producing lightweight vehicles.
“When employing the friction stir scribe technique for joints, we observed a slightly lower corrosion rate,” Joshi noted. “The decline in corrosion rates can be attributed to the emergence of specific high-resistance pathways at the interface during processing. These pathways led to a reduction in the corrosion rate of the magnesium”.
The ability to monitor corrosion with such precision allows researchers to design more accurately rather than overdesign or underdesign components, leading to more efficient and reliable materials for various applications.
CMAP and corrosion mapping services at The Lab
Corrosion costs time and money, with a collective global cost of corrosion to shipowners estimated between $50bn and $80bn.
The Lab’s CMAP service has been put through its paces, analysing corrosion on vessels that have spent time in some of the world’s most testing, brutal environments.
Based on that development background, and its proven credentials, The Lab has received full validation of the PECA method from Lloyd’s Register. It is endorsed for the utilisation of PECA and CMAP on both naval vessels and the entire commercial and merchant fleets.
Contact The Lab about our CMAP services today.
Learn more about our CMAP and corrosion mapping services at The Lab
For more information, industry insights, and the latest news, explore The Lab’s News and Knowledge Hub…
New Efficient Battery Fuel Could Revolutionise Energy Storage | New Ammonia Conversion Marks Leap Forward for Green Hydrogen Energy | Reusable 3D-Printed Glass Bricks Could Cut Construction Emissions
- Author
- Andrew Yarwood
- Date
- 27/02/2025